Full Text Searchable PDF User Manual

GAS-FIRED DOUBLE-EFFECT
ABSORPTION CHILLER-HEATER
This product is a gas-fired absorption unit which provides chilled water for cooling or
hot water for heating in central plant type air conditioning systems. Units with nominal
refrigeration capacities of 30, 40, 50, 60, 80, and 100 tons are complete with operating
and safety controls.
When this equipment is correctly applied, installed in accordance with Yazaki
INSTALLATION INSTRUCTIONS, and properly maintained, it can provide many years
of trouble-free operation.
CONTENTS
GENERAL
Page
ABSORPTION PRINCIPLE
2
COOLING OPERATION
2
HEATING OPERATION
3
CONTROLS
GENERAL INFORMATION
4
CONTROL ADJUSTMENTS
6
OPERATION
COOLING
7
HEATING
7
SAFETY CONTROLS
7
REMOTE CONTROL
7
PRECAUTIONS
7
MAINTENANCE
Page
GENERAL INFORMATION
8
ROUTINE MAINTENANCE
8
MAINTENANCE INTERVALS
8
EVACUATION OVERVIEW
8
CHEMICAL MAINTENANCE
9
WINTER SHUTDOWN
10
TROUBLESHOOTING
10
WATER QUALITY
11
ERROR CODES
11
STARTUP & MAINTENANCE
DATA SHEET
13
WARRANTY
YAZAKI LIMITED EXPRESS
WARRANTY
14
OPERATING INSTRUCTIONS
CH-K30, 40, 50, 60, 80, 100
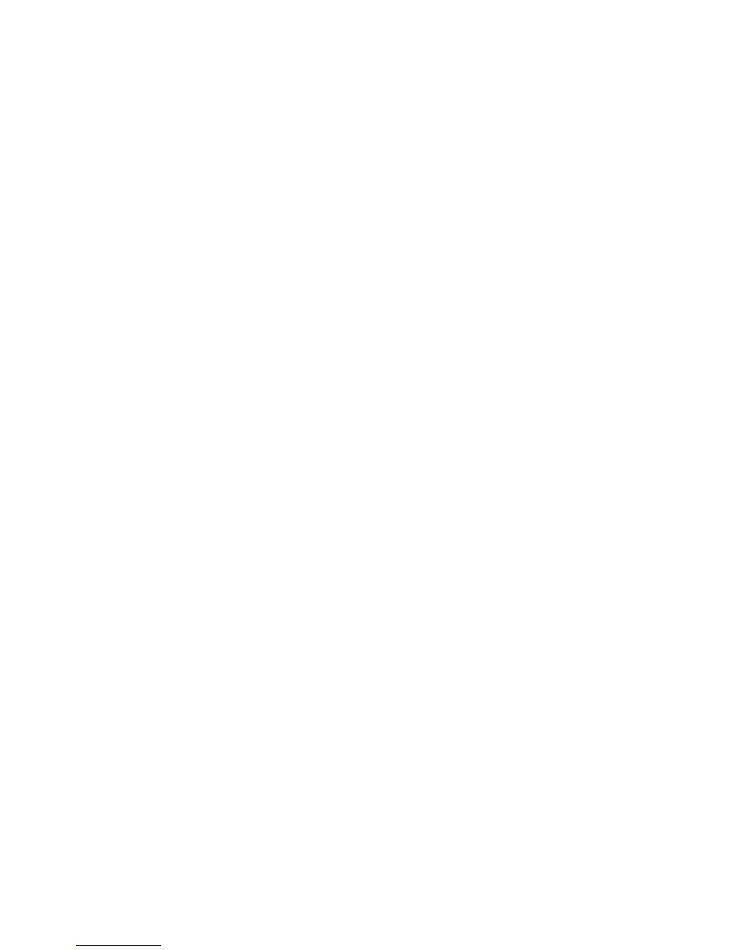
2
GENERAL
These instructions are intended to
acquaint the Owner/End User with the
operation
and
general
maintenance
requirements of Yazaki CH-K gas-fired
double-effect Absorption Chiller-Heaters.
Please read ALL instructions carefully and
observe precautions. Failure to operate and
maintain this equipment in accordance with
the OPERATING INSTRUCTIONS may
affect the equipment performance and
product Warranty.
If the equipment does not operate as
expected, check the Troubleshooting Guide
in these instructions BEFORE calling your
Yazaki Authorized Service Provider
(ASP)
.
This approach will not only save cost but
also avoid any unnecessary downtime.
ABSORPTION PRINCIPLE
Yazaki absorption chiller-heaters use a
solution of lithium bromide and water, under
a vacuum, as the working fluid. Water is the
refrigerant and lithium bromide is the
absorbent.
During cooling operation, refrigerant
liquid boils under the influence of a deep
vacuum in the evaporator and creates a
refrigeration effect which removes heat from
the chilled water circuit.
The double-effect absorption cycle has
two generators, one heated by a burner and
the other heated by superheated refrigerant
vapor. It also utilizes a condenser, an
evaporator, and an absorber.
The absorber and condenser are water
cooled and heat is normally rejected to a
cooling tower, though ground loop is also an
option.
COOLING OPERATION
High Temperature Generator
(HGE)
T
he gas burner heats a dilute lithium
bromide solution in the HE and the boiling
process drives superheated refrigerant vapor
and droplets of semi-concentrated solution
into the primary separator. The semi-
concentrated solution is precooled through a
heat exchanger before flowing into the LGE.
Low Temperature Generator
(LGE)
Superheated refrigerant vapor from the
primary
separator
heats
the
semi-
concentrated
solution
in
the
LGE.
Refrigerant vapor that is liberated from this
solution flows into the Condenser while the
fully concentrated lithium bromide solution is
precooled through another heat exchanger
before flowing to the Absorber.
Condenser
In the condenser, refrigerant vapor is
condensed on the surface of the condenser
tubing bundle and latent heat, removed by
the cooling water, is rejected to a cooling
tower. Refrigerant liquid accumulates in the
condenser and then passes through an
orifice into the evaporator.
Evaporator
In the evaporator, refrigerant liquid is
exposed to a substantially deeper vacuum
than in the condenser due to the influence of
the absorber. As refrigerant liquid flows over
the surface of the evaporator tubing bundle,
it boils and removes from the chilled water
circuit an amount of heat equivalent to the
latent heat of the refrigerant. When at
design condition, the recirculating chilled

3
water is cooled to 44.6°F
(7°C)
while the
refrigerant
vapor
is
attracted
to the
concentrated solution dripping over the
absorber tubing bundle.
Absorber
A deep vacuum in the absorber is
maintained by the affinity of the concentrated
solution from the LGE for the refrigerant
vapor formed in the evaporator. Refrigerant
vapor is absorbed by the concentrated
lithium bromide solution flowing across the
surface of the absorber tube bundle. The
heat of condensation and dilution are
removed by the cooling water and rejected to
a cooling tower. The resulting dilute solution
is preheated through heat exchangers before
the solution pump returns it to the HGE
where the cycle is repeated.
Figure 1
– DOUBLE-EFFECT
ABSORPTION CYCLE (COOLING)
HEATING OPERATION
High Temperature Generator
(HGE)
The solution boils in the HGE and
superheated refrigerant vapor and semi-
concentrated solution flow into the primary
separator in exactly the same manner as in
the cooling cycle.
Low Temperature Generator
(LGE)
In Heat mode, the changeover valve
opens a path for the semi-concentrated
solution to flow out of the primary separator
directly into the Absorber/Evaporator sump.
Therefore,
the
LGE
and
both
heat
exchangers are completely bypassed while
in Heat mode.
Condenser/Absorber
It is imperative that there be NO
COOLING WATER FLOW in the Heat mode.
As such, neither the Condenser nor the
Absorber have any function in Heat mode.
Evaporator
Since the Evaporator acts as the
Condenser in Heat mode, hot refrigerant
vapor condenses on the surface of the
evaporator coil and heat, equivalent to the
latent heat of the refrigerant, is transferred to
the hot water circuit, heating it to a leaving
temperature of 131°F
(55°C)
. The condensed
refrigerant drips off the evaporator and into
the absorber sump where it mixes with the
semi-concentrated solution, diluting it once
again.
Figure 2
– DOUBLE-EFFECT
ABSORPTION CYCLE (HEATING)
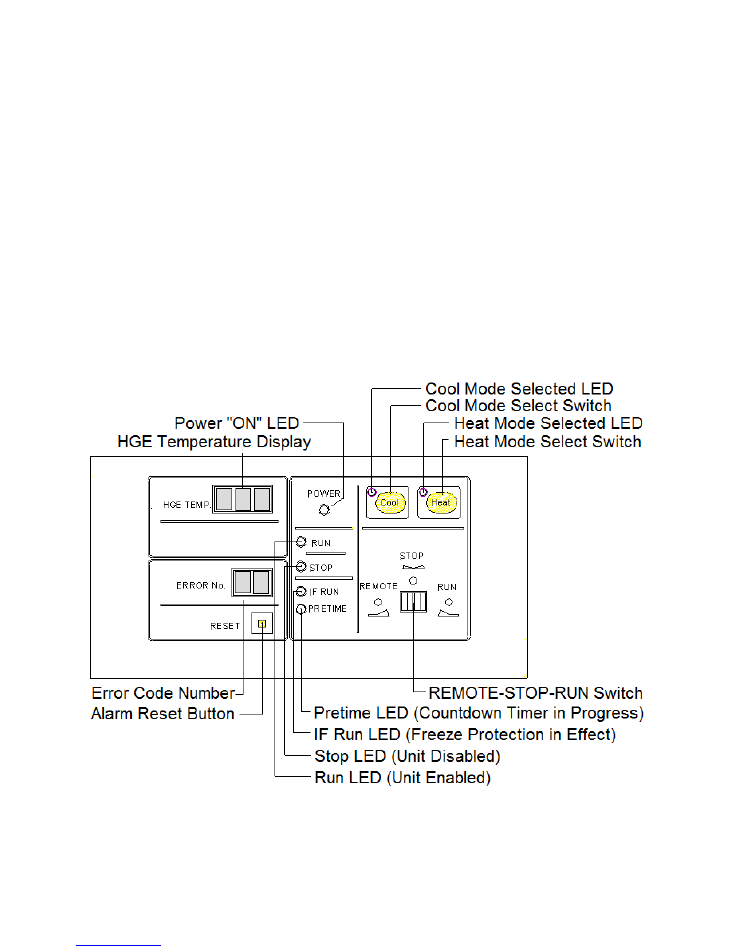
4
CONTROLS
GENERAL INFORMATION
A control panel
(Figure 3)
is built into each
absorption chiller-heater and is located on
the control box, behind the hinged, lower
front-left panel. After inspecting the control
panel and/or making changes to the mode of
operation, make sure that the front panel
closed securely to prevent rain from entering
the cabinet as well as unauthorized
tampering with the controls.
The chiller-heater may also be supervised
and controlled by external control systems to
a limited degree when the necessary
interconnections are installed. Additional
controls and interlocks can be explained by
your ASP.
Once COOLING or HEATING operation is
selected and the unit is started, the chiller-
heater will function automatically and remain
in operation as long as there is a demand for
chilled or hot water.
Be aware that the STOP lamp is lit
anytime the unit is Disabled. The RUN lamp
is lit anytime the unit is Enabled, whether or
not the unit is actively running to control the
chilled or hot water temperature.
Figure 3
– CONTROL PANEL
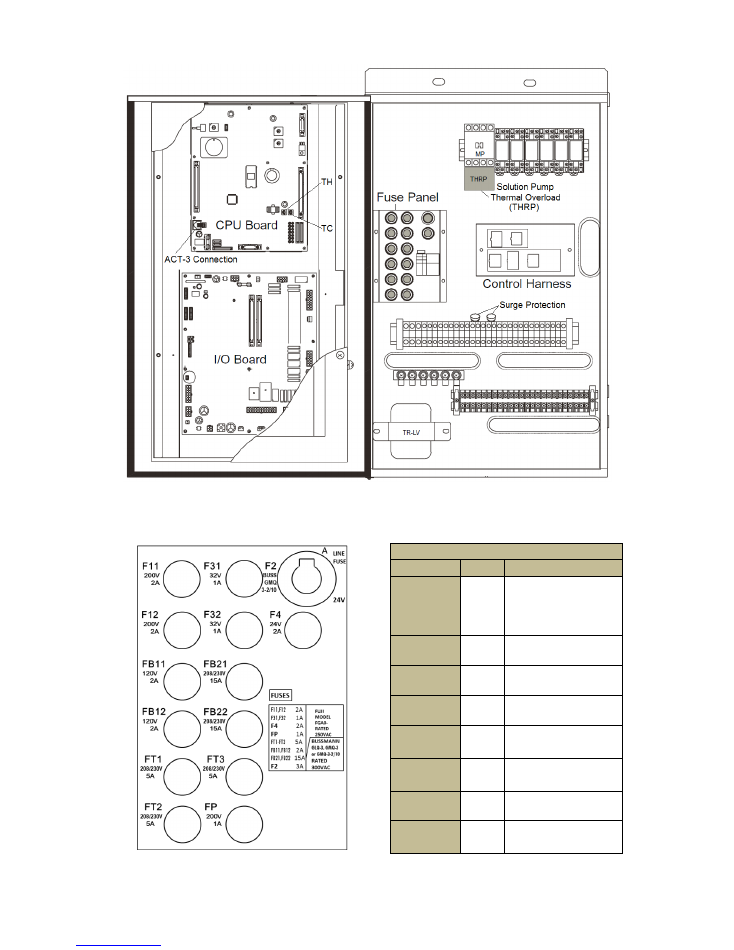
5
Figure 4
– CONTROL BOX LAYOUT
Fuse Rating Chart
Symbol
Amps Replacement
F2
3
Bussmann Model
GLQ-3, GMQ-3 or
GMQ-3-2/10, Rated
300vac.
F4
2
Fuji Model FGAO-2,
Rated 250vac.
F11, F12
2
Fuji Model FGAO-2,
Rated 250vac.
F31, F32
1
Fuji Model FGAO-2,
Rated 250vac.
FB11,
FB12
2
Fuji Model FGAO-2,
Rated 250vac.
FB21,
FB22
15
Nagasawa Model
GAB
FP
1
Fuji Model FGAO-2,
Rated 250vac.
FT1, FT2,
FT3
5
Fuji Model FGAO-2,
Rated 250vac.
Figure 5
– FUSE PANEL

6
Unit Size
THRP Settings (amps)
208v
230v
K30
3.0
2.8
K40
4.5
4.0
K50
4.5
4.0
K60
6.0
5.5
K80
6.0
5.5
K100
6.0
5.5
Figure 6
– SOLUTION PUMP THERMAL OVERLOAD
CONTROL ADJUSTMENTS
The leaving chilled water temperature is
controlled to a standard rating point of
44.6°F
(7°C)
. The operating dead band of
Low Fire is 3.6°F
(2°C)
. The Low Fire dead
band is not adjustable. The operating dead
band of High fire is 7.2°F
(4°C)
. The High
Fire dead band can be cut in half by setting
Dip Switch 2 on the I/O Board to ON. The
leaving chilled water temperature can be
adjusted using the TC potentiometer on the
CPU Board. The leaving chilled water set
point can be set in a range of 40.1°F
(4.5°C)
to 59.9°F
(15.5°C)
.
Similarly, the leaving hot water standard
rating point is 131°F
(55°C)
. The Low Fire
dead band and High Fire dead bands are
identical to Cool mode, but the High Fire
dead band can be cut in half by setting Dip
Switch 4 on the I/O Board to ON. The
leaving hot water temperature can be
adjusted using the TH potentiometer on the
CPU Board. The leaving hot water set point
can be set in a range of 122.9°F
(50.5°C)
to
140.9°F
(60.5°C)
.
Figure 7
– TEMPERATURE CONTROL ADJUSTMENTS

7
OPERATION
COOLING
To engage the unit in Cool mode, press
the COOL button on the Control Panel.
Then choose between RUN and REMOTE
setting. If the unit was not in Heat mode
prior to this point, and the unit is Enabled,
then the unit will engage in cool mode
immediately. If, however, the unit was
previously in Heat mode, the unit will engage
a 30-minute mode change timer and the
PRETIME light will illuminate. Once the 30-
minute timer has expired, the PRETIME light
will go out and the unit will engage Cool
mode immediately.
HEATING
To engage a chiller-heater in Heat mode,
press the HEAT button on the Control Panel.
Then choose between RUN and REMOTE
setting. If the unit was not in Cool mode
prior to this point, and the unit is Enabled,
the unit will engage in heat mode
immediately. If, however, the unit was
previously in Cool mode, the unit will engage
a 30-minute mode change timer and the
PRETIME light will illuminate. Once the 30-
minute timer has expired, the PRETIME light
will go out and the unit will engage Heat
mode immediately.
SAFETY CONTROLS
Safety and limit controls monitor critical
operating conditions within the chiller-heater
and will shut down the unit when abnormal
conditions arise. An Error Code that
designates the cause of the shutdown
(see
Table 2)
is displayed on the control panel.
When the abnormal condition has been
cleared, press the alarm RESET button to
restart the cooling or heating operation. If
Error Code 52 is amongst the codes being
displayed, it will also be necessary to press
the RESET button on the burner controller
itself. If the unit does not restart, then
contact your ASP.
REMOTE CONTROL
The chiller-heater can be Enabled or
Disabled remotely. It can also be instructed
to change between Cool and Heat modes
remotely. No other remote control capability
exists. To enable the unit to be controlled
remotely, switch the unit into REMOTE. The
unit will now Enable or Disable based on the
external connection signals tied into the
Junction Box.
If the unit is in RUN, the unit will ignore
Enable/Disable signals from the remote
signal source, but the unit will still follow
remote Cool/Heat changeover commands
while set to RUN.
PRECAUTIONS
1.
Ensure
that
all
AUTO-OFF-HAND
switches for external pumps and the
cooling tower fan are set in the AUTO
position during normal operation. The
chiller-heater is designed to automatically
control the chilled water pump, cooling
water pump, and cooling tower fan.
2.
At the beginning of the cooling season
clean and refill the cooling tower with
fresh water.
3.
During the winter season the cooling
tower and cooling water circuits should be
drained to avoid freezing and scaling in
the absorber and condenser circuits.
4.
When two or more absorption chiller-
heater modules are installed in parallel,
set all units for the same operating mode.
Leaving water temperature set points may
differ, but operating mode must always be
the same.

8
MAINTENANCE
GENERAL INFORMATION
ALL
MAINTENANCE
SHOULD
BE
PERFORMED
BY
TRAINED
AND
EXPERIENCED PERSONNEL. Your Yazaki
Authorized Service Provider
(ASP)
can help
you establish a standard maintenance
procedure.
For your safety, keep the area around
the equipment clear and free of combustible
materials, gasoline and other flammable
substances. DO NOT obstruct service
access or combustion air supply to the
equipment.
ROUTINE MAINTENANCE
Routine maintenance should be provided
throughout the life of the equipment to
ensure
satisfactory
performance
and
operation.
During the warranty period, an ASP must
be engaged to provide routine maintenance
on chiller-heaters at the beginning of each
cooling season. When the chiller-heater is
used for process cooling or heavy load
operation it may be necessary to schedule
additional service visits to evacuate non-
condensable gases from the vacuum
section.
MAINTENANCE INTERVALS
Every 4 months
(Spring, Summer, Winter)
:
Evacuation
(Units not used in Heat mode can
skip the winter evacuation)
Every 12 months:
Burner Combustion Analysis and Gas
Pressure Check
(Supply and Manifold)
Inhibitor Check
(If required. For the K-Series, an
inhibitor charge is needed every 3 years, on
average.)
Palladium Cell Heater Check
Flow Rate Check
Solution Pump Rotation Check
Flame Rod Replacement
(if required)
Igniter Rod Replacement
(if used and required)
Every 3 years:
HGE Inspection
(pulling the burner to see the
condition inside the HGE)
Average interval for Inhibitor Charge
Average interval for Flame and Igniter Rod
Replacement.
EVACUATION OVERVIEW
Arguably the most important aspect of
maintenance
for
the
chiller-heater
is
maintaining a proper level of vacuum.
Evacuation is performed at the front of the
machine. The evacuation service valves are
referred to as Service Valve A
(upper)
and
Service Valve B
(lower)
.
The evacuation service valves are back-
seating access valves similar to those used
throughout the refrigeration industry. The
stem has a 10mm square head. The stem
secures a copper seal to a steel seat inside
the valve. Do not over-torque this valve or
else the seal can become damaged and
compromise vacuum integrity. The proper
torque is 14.75 ft-lbs
(20 Nm)
. Yazaki offers a
torque wrench
(P/N N7510)
specifically for
use with this service valve.
A number of precautions should be
observed at all times during evacuation.

9
*** Great care must be taken to ensure
that no oil enters the Yazaki chiller-
heater! Permanent damage could result
from even a small amount of oil being
introduced into the vacuum section! ***
Never
leave a vacuum pump running
unattended. Power loss could allow the
chiller-heater vacuum section to suck oil
out of the pump in a matter of seconds.
Never
have the Service Valve open
unless the vacuum pump is running and
the integrity of the vacuum lines between
the valve and the pump has been verified
as tight.
Never
have the vacuum pump discharge
tube in the water bucket unless the
vacuum pump is running. The vacuum
pump could suck water from the bucket
and contaminate the oil charge.
Never
pull
an
extended
vacuum
(exceeding a few hours)
. If such seems to
be necessary, there is likely to be
something wrong with the vacuum pump
or the oil has been contaminated with
moisture inherently found inside the
chiller-heater vacuum section.
Always
start with a fresh oil charge in the
vacuum pump.
Always
use a liquid trap or collection
flask.
Always
use a vacuum gauge to verify the
level of vacuum achieved. Run time has
almost nothing to do with the level of
vacuum achieved.
Use only dual-stage, deep vacuum
pumps. Typical refrigeration vacuum pumps
may not perform well on a vessel as large as
the chiller-heater
’s vacuum section. Just
because the vacuum pump has stopped
producing bubbles in the water bucket does
NOT mean the vacuum level is adequate. A
digital vacuum gauge MUST be used in
order to determine the true level of vacuum
achieved.
The desired level of vacuum on a
machine that is not running would be less
than 2000 microns
(<2 mmHg)
, with less than
1000 microns
(<1 mmHg)
preferred. On a
machine actively running in Cool mode
(currently attempting to satisfy chilled water loop
load)
, the desired level of vacuum is 4000-
5000 microns
(4-5 mmHg)
, no less. Any lower
than that on a running machine can cause
the
vacuum
pump
to
remove
an
extraordinary amount of refrigerant vapor
(water)
.
A
step-by-step,
detailed
evacuation
method is provided in the Service Manual.
The general evacuation assembly setup is
displayed in Figure 9.
Figure 9
– GENERAL EVACUATION
ASSEMBLY SETUP
CHEMICAL MAINTENANCE
It is not necessary to perform regular
chemical maintenance on the Yazaki
chiller-heater itself.
The
chemical
balance
has
been
established in the factory during run testing.
Normally, the only chemical that must be
maintained is the inhibitor charge. By
capturing
non-condensable
gases,
comparisons can be made to determine if
the normal hydrogen byproduct is being
produced at anticipated rates. If more
hydrogen is being produced than anticipated,
a maintenance inhibitor charge may need to
be introduced into the machine by the ASP.
An inhibitor charge is typically needed every
three
(3)
years in Yazaki gas-fired chiller-
heaters.
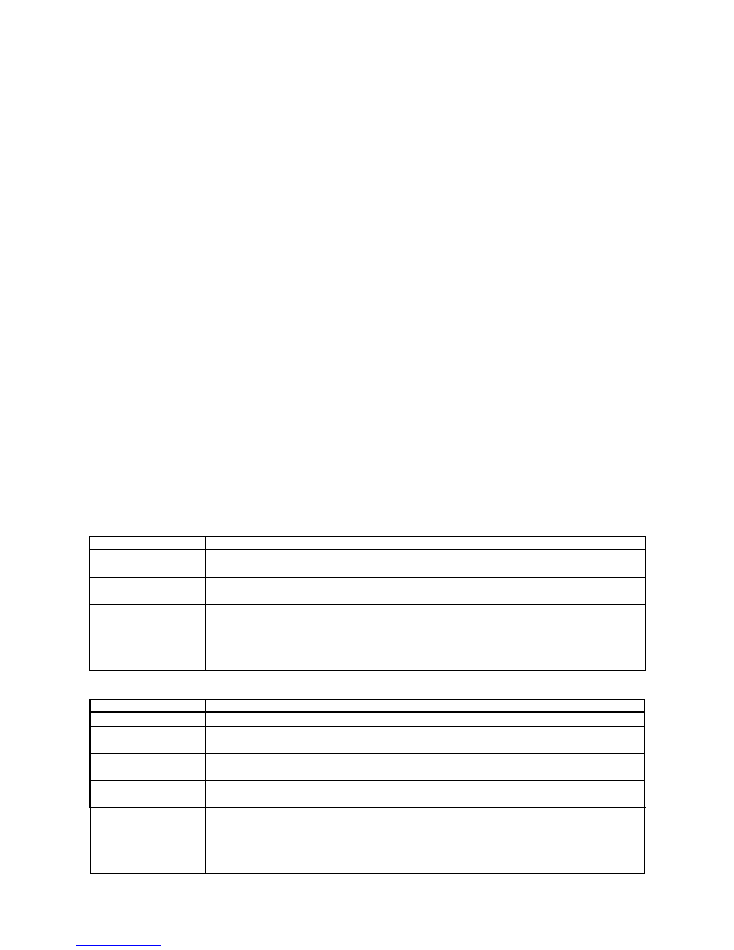
10
SHUTDOWN
The fluids within the chiller-heater itself
need no preparation for freezing conditions.
Only the fluids in the chilled water and
cooling water circuits need to be addressed
during potentially freezing conditions.
When the equipment is located outdoors
in climates subject to freezing, cooling water
should be drained from the chiller-heater,
fluid circuit piping, and cooling tower at the
end of the cooling season. Use glycol of
adequate concentration in the chilled water
and heat medium circuits to prevent freeze
damage. The glycol will reduce the cooling
and heating capacity but this may be offset
somewhat by increasing the circuit fluid flow
rate. If in doubt about potential freeze
damage in your area, discuss it with your
ASP. Damage to the unit due to freezing is
not covered by the product warranty.
If a unit is to be shut down for the winter,
but no fluid circuits are to be drained, then
simply Disable the chiller-heater and allow
the unit to complete its Post Dilution Cycle.
Once completed, it is safe to leave the unit
as it sits for the off-season. Take
appropriate measures to ensure the fluids in
all fluid circuits are protected from freezing
(glycol, heat tape, etc.)
.
If a chiller-heater is to be shut down long-
term, then fluid circuits should be drained.
Disable the chiller-heater and allow the unit
to complete its Post Dilution Cycle. Once
completed, turn off the breaker on the unit
control panel. Then drain each fluid circuit.
Once drained, make sure to blow in both
directions
through
each
circuit
with
compressed air
(or similar)
to make sure no
significant amount of liquid remains inside
them. Close all isolation valves so as to
isolate the unit from the rest of the respective
fluid circuit. Pressurize each fluid circuit in
the chiller-heater with dry nitrogen to a
pressure of 1-2 PSI (7-14 kPa) to help inhibit
corrosion in the circuit during storage. It may
be desirable to break the vacuum in the
chiller-heater itself as well. If doing so,
pressurize the unit to the same pressure as
the circuits using nitrogen. See the Service
Manual for further details.
TROUBLESHOOTING
SYMPTOM: Chiller-heater does not operate.
Possible Cause
REMEDY
No High Voltage
Check the LED for the Power indication on the Control Panel. If it is not illuminated, check the
main power disconnect, fuses, and breakers.
Solution Pump Not
Running
Check the THRP overload switch. Check the GP temperature. Until the GP temperature rises
above 190°F
(88°C)
, the solution pump may remain off until the GP temperature warms up.
Chiller-heater is not
running but WTO
temperature is above
set point.
Nothing may be wrong. If the system chilled water loop has satisfied by reaching the desired set
point, the unit will shut down until the WTO sensor reads a temperature 3.6°F
(2°C)
above the set
point temperature, no matter how long that may take. To force operation, turn off power to the
chiller-heater, leave power off for 10 seconds, and then restore power. The chiller-heater should
start up if the WTO sensor reading is above the set point.
SYMPTOM: Poor cooling capacity.
Possible Cause
REMEDY
Poor Vacuum
Evacuate the machine per normal maintenance procedure. A leak check may also be necessary.
High Inlet Cooling
Water Temperature
Check the cooling tower fan. Check the cooling tower fluid level.
Low Cooling Water
Flow Rate
Check the cooling tower sump and cooling water circuit strainers.
Condenser/Absorber
Fouling, Scale Buildup
Check the cooling water circuit strainers. A chemical de-scaling procedure will be necessary.
Everything appears
normal but the leaving
chilled water
temperature is too
high.
Nothing may be wrong. If the load of the chilled water circuit exceeds the capacity of the chiller-
heater, the system will find equilibrium at a higher leaving chilled water temperature. If the
temperature drop through the chilled water loop is approximately 8-12°F
(4-6°C)
, then the unit
may actually be giving its full capacity and its capacity simply may not be enough. Check for
reasons that the load may have artificially increased
(open doors, new equipment, leaking valves, etc.)
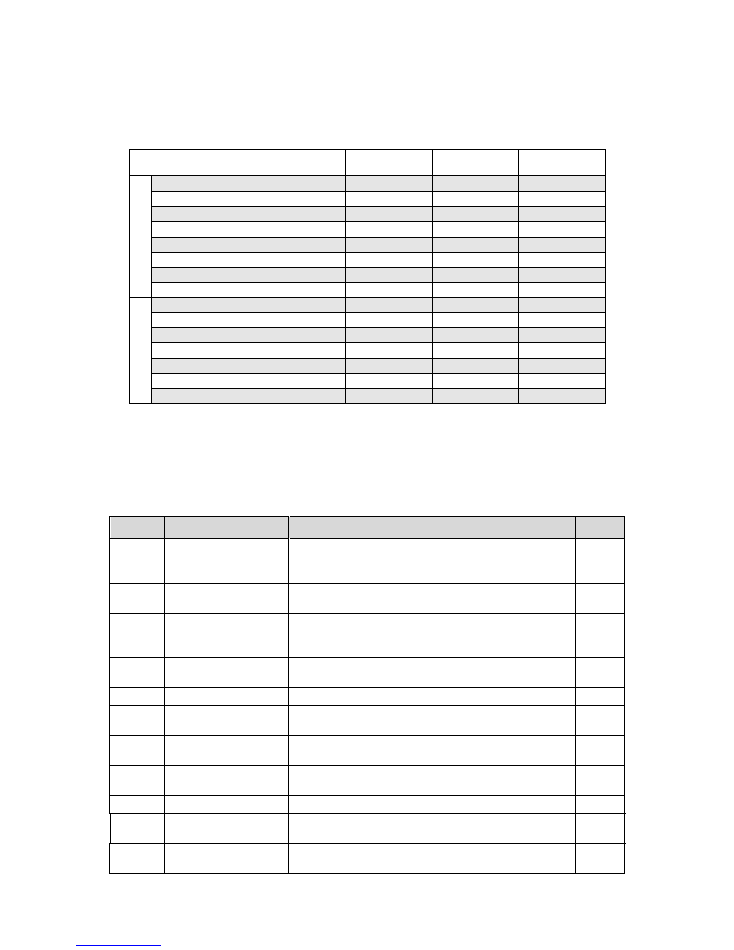
11
WATER QUALITY
It is the End User’s responsibility to have the
cooling water analyzed and chemically treated as
often as necessary so that it conforms to the
limits specified in Table 1. The water quality in
the chilled water, cooling water, and heat medium
circuits shall not exceed the following limits:
ITEM
CHILLED
WATER
COOLING
WATER
MAKE-UP
WATER
S
tand
ar
d
pH (at 77°F)
6.8 - 8.0
6.5 - 8.2
6.8 - 8.0
Conductivity (
S/cm at 77°F)
400
800
300
Chloride ion (Cl
-
ppm)
50
200
50
Sulfate ion (SO
4
2-
ppm)
50
200
50
M-alkalinity (CaCO
3
ppm)
50
100
50
Total hardness (CaCO
3
ppm)
70
200*
70
Calcium hardness (CaCO
3
ppm)
50
150
50
Ionic silica (SiO
2
ppm)
30
50
30
Ref
er
en
ce
Total iron (Fe ppm)
1.0
1.0
0.3
Copper (Cu ppm)
1.0
0.3
0.1
Sulfide ion (S
2-
ppm)
ND
ND
ND
Ammonium ion (NH
4
+
ppm)
1.0
1.0
0.1
Residual chlorine (Cl ppm)
0.3
0.3
0.3
Free carbon dioxide (CO
2
ppm)
4.0
4.0
4.0
Ryzner stability index
-
6.0 - 7.0
-
NOTES:
1.
ND (Not Detectable)
2.
*Total hardness of make-up water shall not exceed 70 ppm when bleed off is the only method used to control water quality.
Table 1
– WATER QUALITY REQUIREMENTS
ERROR CODES
Error Code
Number
Error Description
Notes
Reset
Type
FS
Flow switch alarm
Chilled/hot water flow switch FS1 open, but for less
than 10 minutes. After 10 minutes, this changes
automatically to error code 27.
Auto
01
DCP power error
Optional AroTrend remote monitoring package has
lost power.
Auto
02
DCP communication
line short
Power available to the optional AroTrend remote
monitoring package but communications line is
shorted.
Auto
03
DCP communication
line noise
Optional AroTrend Remote monitoring package
cannot communicate with the chiller-heater.
Auto
04
Accessory error
Optional fire safety shutdown.
Manual
05
Chilled/hot water
pump interlock error
Voltage signal from terminal CM2 in the junction box
is not returning to terminal 3 in the junction box.
Manual
06
Cooling water pump
interlock error
Voltage signal from terminal CM2 in the junction box
is not returning to terminal 4 in the junction box.
Manual
07
Cooling tower fan
interlock error
Voltage signal from terminal CM2 in the junction box
is not returning to terminal 5 in the junction box.
Manual
08
Solution pump error
Solution Pump overload THR1 has tripped.
Manual
09
Generator (HGE) over
heat error
The GP sensor has reported a temperature in excess of
325.4°F
(163°C)
. Unit locks out.
Manual
10
Generator (HGE)
temp error
GPSC has opened. Unit locks out.
Manual
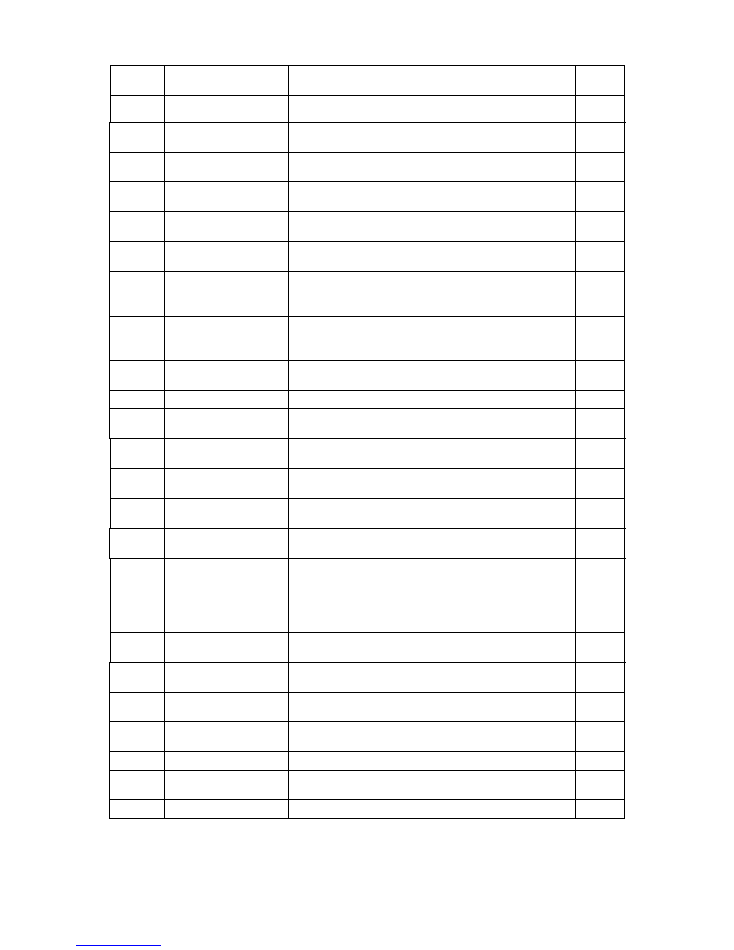
12
12
Generator (HGE)
solution level error
GLS reports open. Ignored for the first 30 seconds and
ignored after 20 minutes of operation. Unit locks out.
Manual
13
WTO sensor error
WT sensor reads below 14°F
(-10°C)
or above 212°F
(100°C).
Auto
18
Seismic switch error
Optional seismic switch is open when it should be
closed.
Manual
20
Cooling water scale
alarm
CND - CTO > 7.2°F
(4°C)
No Reset
Required
21
Cooling water scale
error
CND - CTO > 12.6°F
(7°C)
Manual
25
High cooling water
temperature
Cooling water above acceptable temperatures: CTO
above 108°F
(42°C)
for 3 consecutive minutes.
Auto
26
Generator (HGE) over
heat in heating mode
GPSH has opened. Unit locks out.
Manual
27
Chilled/hot water
flow switch error
(FS1)
FS1 open when it should be closed. Condition has
existed for more than 10 minutes.
Auto
28
Cooling water flow
switch error (FS2)
Optional cooling water flow switch (FS2) open when it
should be closed. Condition has existed for more than
10 minutes.
Auto
29
CTO sensor error
CTO sensor reads below 14°F
(-10°C)
or above 212°F
(100°C)
. Ignored for first 10 minutes of P2 operation.
Manual
32
GP sensor error
GP sensor reads above 338°F
(170°C)
. Unit locks out.
Manual
33
CTI sensor error
CTI sensor reads below 14°F
(-10°C)
or above 212°F
(100°C)
. Ignored for first 10 minutes of P2 operation.
Manual
36
CND sensor error
CND sensor reads below 14°F
(-10°C)
or above 212°F
(100°C)
.
Auto
40
Loss of cooling
capacity
LT temperature reading has not fallen below 59°F
(15°C)
within 30 minutes.
Manual
41
Cooling mode
interrupt error
CIR contacts open for 20 consecutive seconds when
they should be closed.
Manual
42
Heating mode
interrupt error
HIR contacts open for 20 consecutive seconds when
they should be closed.
Manual
43
Low cooling water
temperature
CTI sensor reads below 46.4°F
(8°C)
at start of
operation, or has dropped below this limit for 2
consecutive minutes during operation. Burner shuts
down. P1 and P2 continue to run. Burner starts up
again once CTI sensor rises above 48.2°F
(9°C).
Auto
44
Changeover valve
error
Changeover valve end switch has not closed within 22
seconds.
Manual
52
Combustion system
error
Burner Controller indicates an alarm condition.
Manual
72
LT sensor error
LT sensor reads below 14°F
(-10°C)
or above 212°F
(100°C)
.
Manual
88
Circuit Board Error
Either the CPU Board or the I/O Board or both are not
responding. All functions frozen.
Not
Possible
93
Model setting error
DS1 and DS3 settings are incompatible
Manual
94
TS1 Position Error
Unit left in BC or VC test mode without interaction
longer than 30 minutes.
Auto
95
Data Error
CPU board requires reboot or replacement.
Manual
Table 2 - ERROR CODES
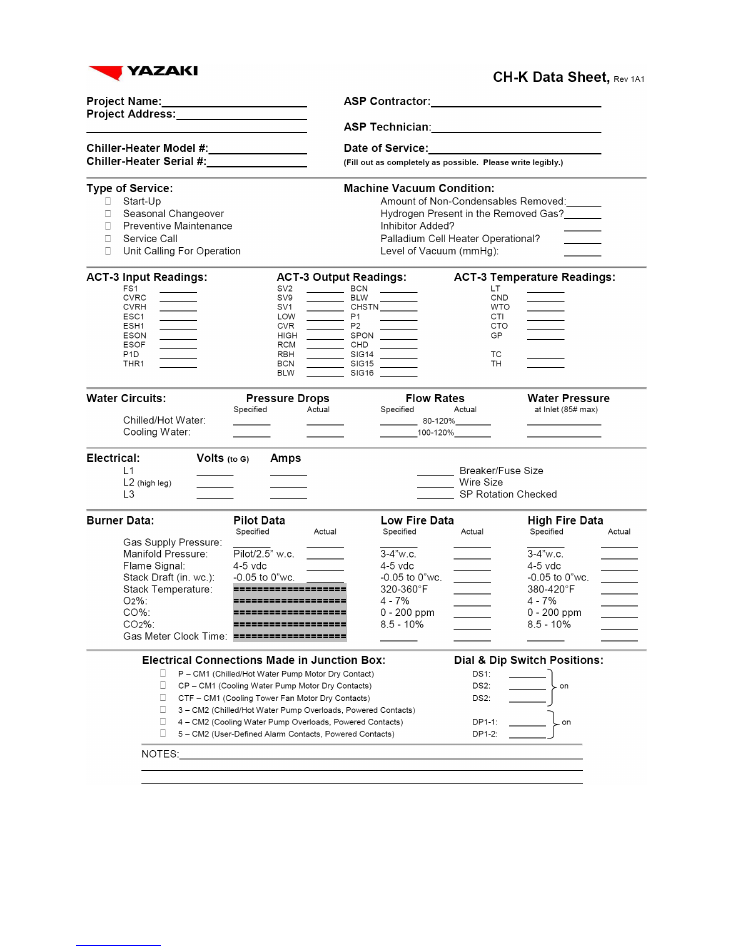
13
Please send a copy of any maintenance data sheets to Yazaki Energy Systems, Inc., at the
address, FAX number, and/or email address listed on the last page of this document.

14
WARRANTY
YAZAKI LIMITED EXPRESS
WARRANTY
1.
SCOPE OF COVERAGE.
The Limited Express Warranty of Yazaki
Energy Systems, Inc. (“YESI”) applies to the initial retail
purchaser and assigns (“CUSTOMER”) of Yazaki double-effect
chiller-heaters and water-fired chillers and chiller-heaters
(“PRODUCT”) installed in the U.S.A., Canada, and all other
countries within the YESI sales territory at the time of sale of
the PRODUCT. The initial retail purchaser may assign its
rights under this Limited Express Warranty to any third party
with prior written consent by YESI which shall not be
unreasonably withheld by YESI.
2.
GENERAL EXPRESS WARRANTIES.
YESI warrants to the
CUSTOMER, that the PRODUCT shall be free from defects in
material and workmanship which are discovered and
reported in writing to YESI within the period of one (1) year
(“Original Warranty Period”) from the time when the
PRODUCT is initially placed into operation at the CUSTOMER’s
facility (“Start-Up Date”), or two (2) years from the date of
manufacture, whichever expires first, and subject to the
disclaimers and limitations of this Limited Express Warranty.
As a condition of this Limited Express Warranty, the
CUSTOMER shall arrange at its own cost for annual routine
maintenance of the PRODUCT, prior to cooling operation and
prior to heating operation of the PRODUCT, by a service
provider authorized by YESI, in accordance with the Yazaki
Operating and Maintenance Instructions.
This is not a warranty of performance, but a limited warranty
as to the condition of the PRODUCT at the Start-Up Date.
3.
DISCLAIMER AND LIMITATION OF EXPRESS WARRANTIES.
There are no express warranties other than those contained
in this Limited Express Warranty.
4.
WARRANTY REGISTRATION CARD.
Every new PRODUCT is
accompanied by a Warranty Registration Card which shall be
completed, signed by an authorized representative of the
CUSTOMER, and returned to YESI. This Limited Express
Warranty shall not apply unless the Warranty Registration
Card is fully completed and returned to YESI within thirty (30)
days of the Start-Up Date of the PRODUCT.
5.
WARRANTY SERVICE.
All routine maintenance, parts
replacement, and vacuum section repairs of the PRODUCT
during the Original Warranty Period must be performed by a
service provider authorized by YESI.
To obtain warranty service, contact:
a.
The Service Provider indicated on the Warranty
Registration Card, or if that person is not available;
b.
YESI’s Distributor or Sales Representative from whom
the PRODUCT was purchaced, or if that person is
not available;
c.
Yazaki Energy Systems, Inc.
6.
REMEDY DURING ORIGINAL WARRANTY PERIOD.
YESI shall,
at its sole discretion, repair or replace the PRODUCT or parts
there-of which YESI shall determine upon examination to be
defective or not in conformity with the Original Warranty
contained herein (“Defective Part”), subject to the terms
hereof. YESI shall supply by standard ground transportation
all parts required to repair or replace any Defective Part and
shall pay the authorized service provider the necessary and
allowable labor charges as fixed in YESI’s warranty service
payment schedule in effect from time to time (“Fixed Labor
Charges”). The CUSTOMER shall be solely responsible for all
labor costs or charges in excess of the Fixed Labor Charges. A
copy of the current Fixed Labor Charges for warranty service
can be obtained by an authorized service provider upon
written request to YESI.
7.
LIMITATION OF WARRANTY AND LIMITATION OF REMEDY.
CUSTOMER’s remedies shall be limited (even in the event of
YESI’s default of its warranty obligations) exclusively to those
provided in section 6 of this Limited Express Warranty.
UNDER NO CIRCUMSTANCES SHALL YESI BE LIABLE FOR
CONSEQUENTIAL OR INCIDENTAL DAMAGES. If the limitation
of liability fails the essential purpose, CUSTOMER’s liability
shall be expanded to the minimum extent to avoid failure of
the essential purpose. Customer waives any cause of action
or theory of liability including, but not limited to, those
arising under contract, tort, strict liability, product liability,
statutes, or otherwise, except as specifically provided by the
UCC as modified and limited herein. The warranty period of
all replacement parts and PRODUCTS shall be deemed to
commence on the Start-Up Date of the original PRODUCT, not
the installation date of the replacement part or PRODUCT,
and YESI’s warranty obligation hereunder shall not be
extended by virtue of such replacement.
8.
DISCLAIMER OF IMPLIED WARRANTIES.
YESI DISCLAIMS
ALL IMPLIED WARRANTIES (OTHER THAN GOOD TITLE)
INCLUDING, BUT NOT LIMITED TO, THOSE OF FITNESS FOR A
PARTICULAR PURPOSE, MERCHANTABILITY, AND NON-
INFRINGEMENT. There are no warranties which extend
beyond those express warranties contained in this Limited
Express Warranty. CUSTOMER affirms that it has not relied
upon YESI’s skill nor judgment to select or furnish PRODUCT
for any particular purpose. YESI does not warrant that the
PRODUCT complies with the requirements of any safety or
environmental code or regulation of any federal, state,
municipality, or other jurisdiction beyond the specific express
warranties in this Limited Express Warranty.
9.
SPECIFIC EXCLUSIONS.
In addition to all other exclusions
contained in this Limited Express Warranty, YESI’s warranty
shall also not apply under the following circumstances:
a.
Damage to the PRODUCT caused by an un-authorized
service provider;
b.
Defect in any part not supplied or authorized by YESI;
c.
Installation or operation of the PRODUCT in any way not
described in the applicable Yazaki Installation and
Operating Instructions;
d.
Applications for process cooling (except single-effect
absorption chillers);
e.
Failure to provide routine maintenance of the PRODUCT
by a Yazaki-authorized service provider in accordance
with the applicable Yazaki Operating and Maintenance
Instructions;
f.
Failure to maintain the quality, flow, and supply
temperature of the cooling water in accordance with
Yazaki standards and limitation;
g.
Damage caused to the PRODUCT from freezing,
overpressure, and corrosion in any water circuit;
h.
Misuse, abuse, negligence, accident, natural disaster,
alteration, misapplication, or experimental use of the
PRODUCT;
i.
Normal fading and minor deterioration of the cabinet
surface caused by exposure to the elements;
j.
Removal of the PRODUCT from its original installation site
unless the relocation is approved in writing by YESI prior
to the act of relocation;
k.
Materials, such as inhibitor and batteries, that are
consumed during normal operation of the PRODUCT;
l.
Damage to other products outside the PRODUCT, not
supplied by YESI, caused by use of materials that are not
compatible with the operating characteristics of the
PRODUCT, regardless of the absence of specific
instructions in Yazaki Installation and Operating
Instructions.
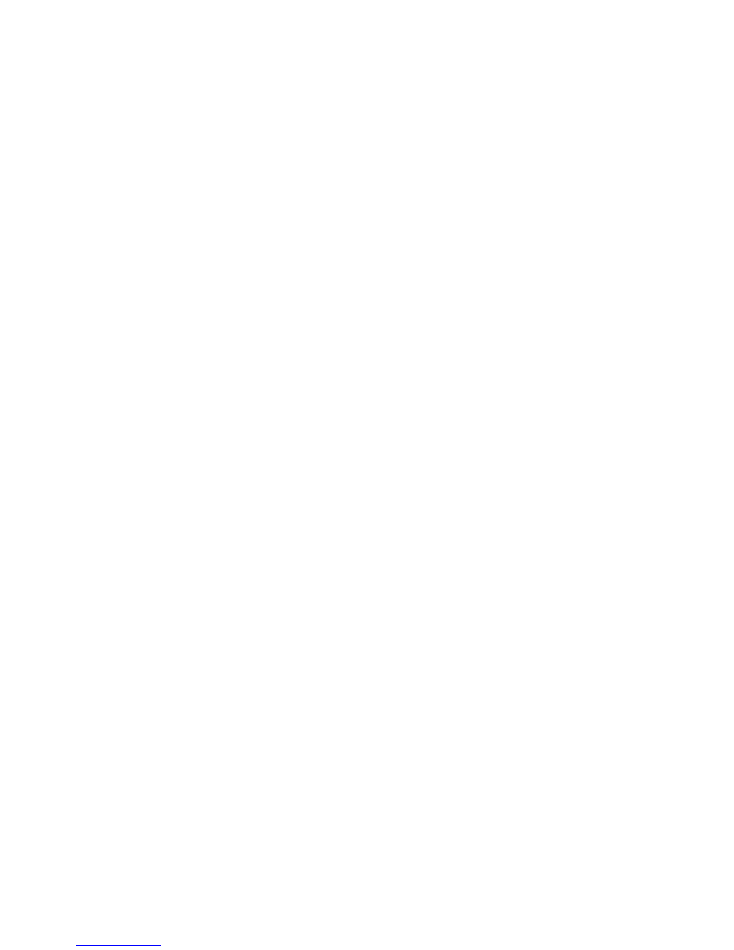
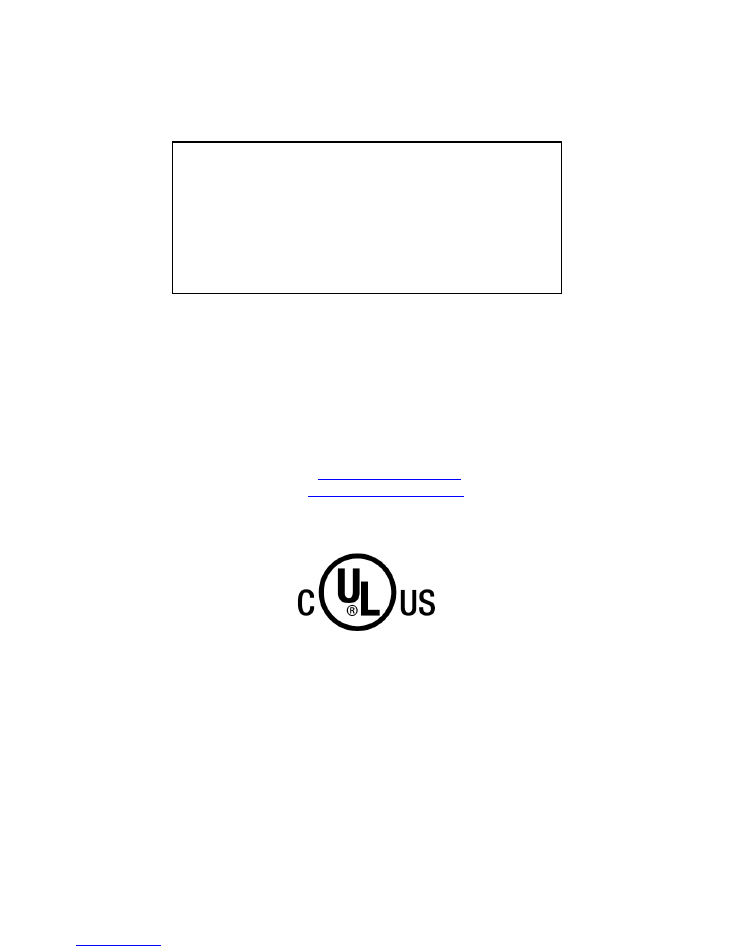
16
YAZAKI AUTHORIZED SERVICE PROVIDER
For information concerning service, operation
or technical assistance, please contact your
Yazaki Authorized Service Provider or the following:
YAZAKI ENERGY SYSTEMS, INC.
701 E PLANO PKWY, SUITE 305
PLANO, TEXAS
75074-6700
Phone: 469-229-5443
Fax: 469-229-5448
Email:
yazaki@yazakienergy.com
Web:
http://www.yazakienergy.com
This symbol on the product’s name plate means it is listed by
UNDERWRITERS LABORATORIES, INC.
Yazaki reserves the right to discontinue, or change at any time,
specifications or designs without notice and without incurring obligations.
KUL-OM1-1A-1011