Full Text Searchable PDF User Manual
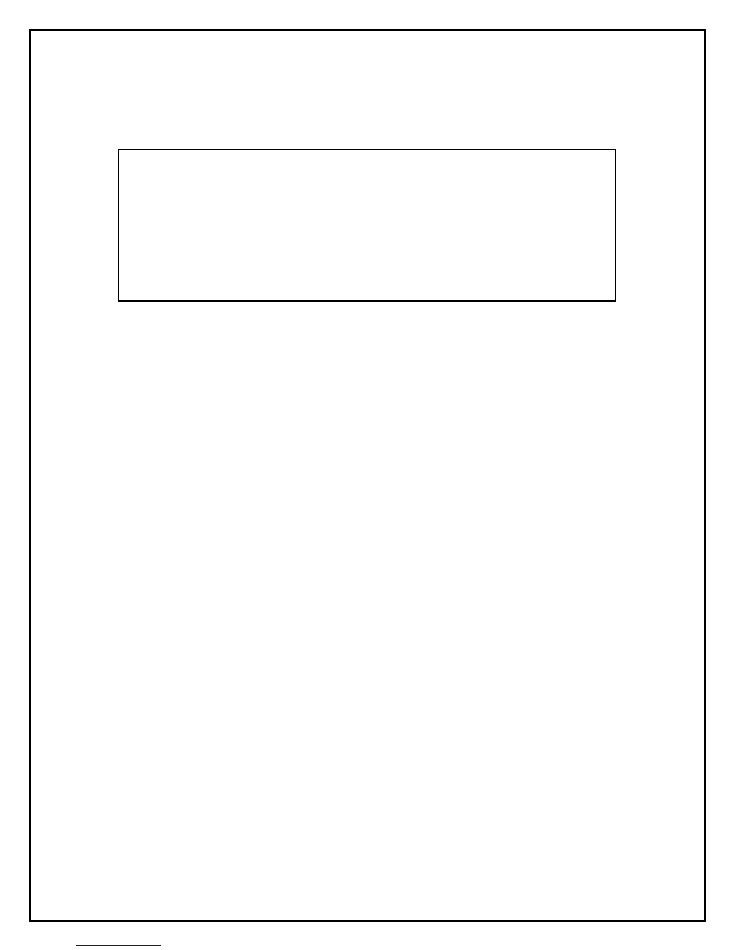
THERMOTRON
Thermo-Dynamics
ROUTE
61
•
P.
O.
BOX
325
•
SCHUYLKI
LL
HAVEN,
PA
17972
•
(
570)
385-
0731
•
FAX
(
570)
385-
5304
www.thermodynamicsboiler.com
Operation
Maintenance
and
Installation
Instructions
Models OTF / ITF

Contents
General Information ......................................................................................................1
Service Policy ................................................................................................................1
Installation Instructions .................................................................................................2
Filling Instructions .........................................................................................................2
Winterizing .....................................................................................................................3
Start-Up and Operation ................................................................................................3
Piping/Connection Diagrams .......................................................................................4
Assembly Diagrams ......................................................................................................5
Trouble Shooting ..........................................................................................................6
Care and Maintenance .................................................................................................6
Pool Coil Diagram .........................................................................................................7
Wiring Diagrams ...........................................................................................................8
Parts List ........................................................................................................................9
Specifications ..........................................................................................................10
Home Owner Information .......................................................................................11
Set-Up and Service Records ..................................................................................12
Warranty Information ..............................................................................................12
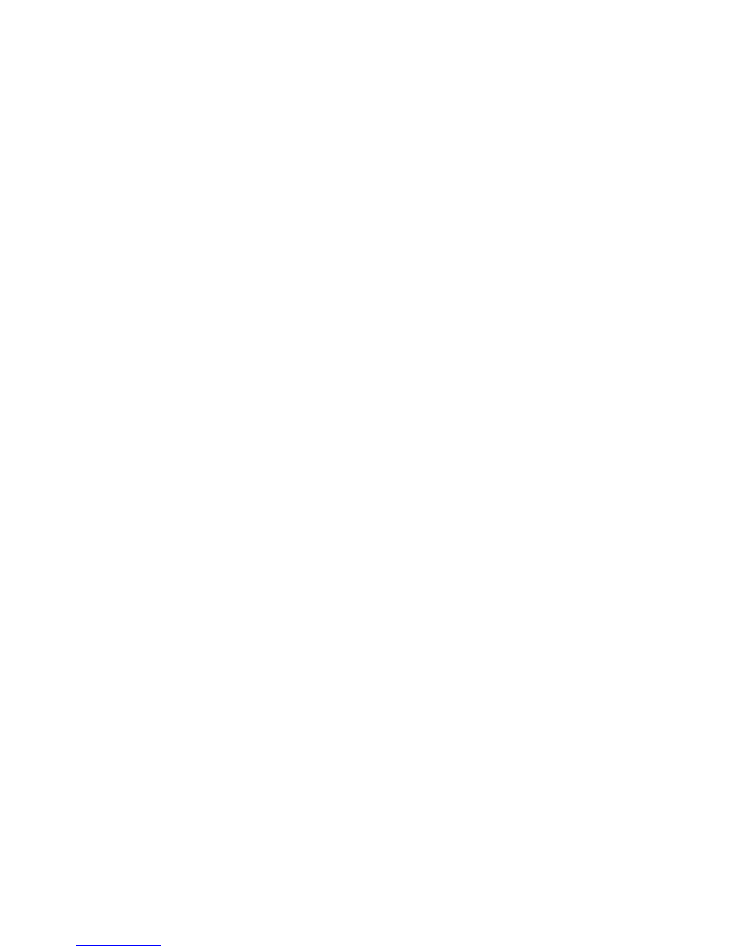
1
G e n e r a l I n f o r m a t i o n
1) Please read all instructions and review all diagrams prior to proceeding with installation.
2) Instructions and diagrams are intended only as guidelines.
3) Installations must conform with all applicable national, state and local codes.
4) Additional guidelines are available from National Fire Protection Association (NFPA), American
society of Mechanical Engineers (ASME) and Building Officials and Code Administrators
(BOCA).
S e r v i c e P o l i c y
Congratulations on the purchase of your new pool heater. Here at Thermo-Dynamics Boiler
Company we pride ourselves on the design and construction of our product. Our intent is to furnish
you with a high quality appliance that will provide you and your family with years of trouble free
service.
In order to maintain peak performance of your pool heater, it is recommended that the unit be win-
terized at the end of the season and that the burner/boiler be serviced annually. Servicing of your
appliance must be performed by a qualified heating technician. You should utilize a qualified heat-
ing technician familiar with your installation to manage your heater and perform periodic mainte-
nance. Proper care and maintenance of your pool heater will allow you to enjoy the benefits of your
new purchase as well as extend its long useful life.
In the event that your serviceman encounters difficulty with the pool heater, he/she shall contact
the distributor from which the product was purchased. The distributor shall, in turn, contact the
Thermo-Dynamics sales representative for your area. By adhering to this protocol, Thermo-
Dynamics wishes to provide you with responsive and unparalleled service. We realize the impor-
tance that our product means to you and your family and our goal is to get your heater up and run-
ning as quickly as possible.
Thank you for purchasing the Thermo-Dynamics pool heater. Again, it is our intent to provide you
with a high quality trouble free product that will be part of your family for many years to come.
Please consider Thermo-Dynamics Boiler Company in the future for all of your home heating
needs.
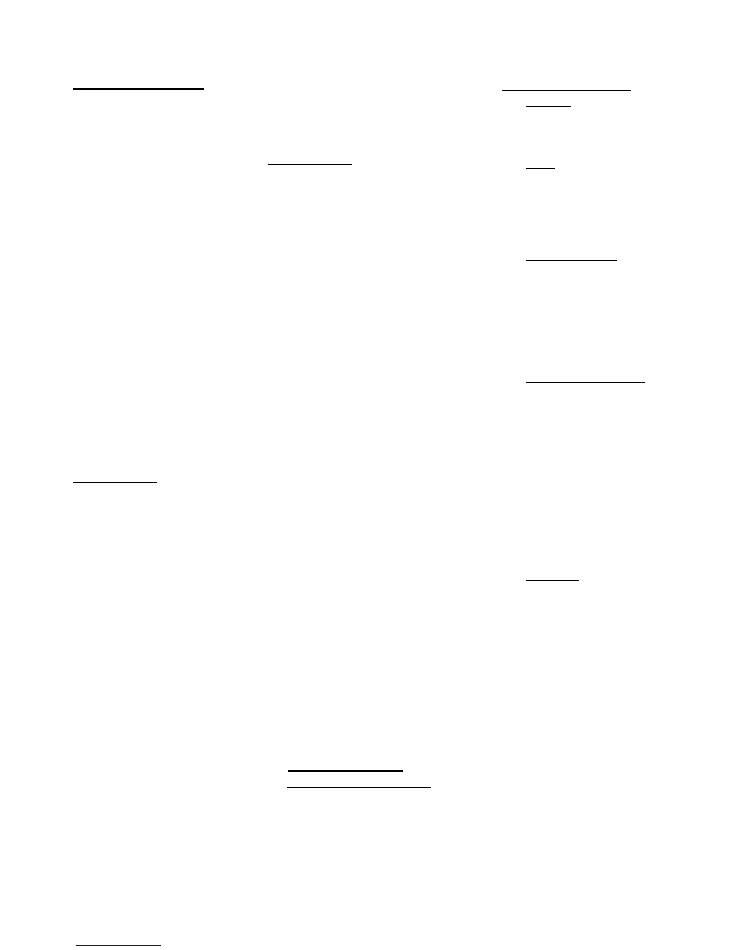
2
Section I. Installation Instructions
Control of combustion draft.
(1) Locating The Heater:
Before uncrating the unit prepare
the location. It should be placed upon
a good level concrete floor or pad.
Care should be taken to locate the
unit for easy accessibility. Please
maintain the following clearances to
combustible materials:
OTF
(Outdoor Pool Heaters)
Front 24 inches
Back 24 inches
Sides 12 inches
ITF
(Indoor Pool Heaters)
Front 24 inches
Back 12 inches
Sides 12 inches
In addition, the air openings in the
cabinet shall have adequate clearance
to allow for sufficient air intake to the
burner. Uncrate the unit as close to
its permanent location as possible to
prevent handling damage.
(2) Connections:
Do not run any piping along the
front access panel of heater as they
may interfere with servicing. The tap-
pings for connecting the unit to the
pool circulation lines are at the back of
the heater. These connections are 1-
1/2" NPT. Connections should be
made as per the piping illustration on
page 4. Install unions at the heat
exchanger so it can be readily
removed for service. If plastic pipe is
used, make connection to the unit with
metal piping and run metal piping to
the floor line before joining to plastic
pi
pe.
Thi
s
wi
l
l
ac
t
as
a
“
heat
-
t
r
ap”
and
reduce possible damage to the plastic
pipes from overheating. Install posi-
tive check valve on inlet side. Install a
Tee joint at the coil where the PIPING
FROM the pool filter/pump ENTERS
the coil. Install the copper well provid-
ed into the piping Tee and insert the
remote sensing bulb from the L-4031
pool thermostat.
An adjustable by-pass around the
heat-exchanger is required. The by-
pass is an important and necessary
component to obtaining optimum
performance (see piping diagram on
page 4). In order to properly adjust
the flowrate through the system,
please adhere to the following steps:
By-Pass Set-Up
a) Use piping and full-size valve
t
o
c
onnec
t
t
he
“
I
n”
and
“
Out
”
s
t
r
eams
of the pool coil.
b) With the bypass valve wide
open take a pressure reading at the
gauge on the pool filter.
c) Pressure reading with bypass
valve full open is the baseline pressure.
d) Slowly close the bypass valve
so that the pressure increases.
e) Stop when pressure reaches 2
to 4 psi above the baseline at the filter.
Alternatively, flowrate may be set
by comparing the temperature differ-
enc
e bet
ween t
he “
I
n”
and “
Out
”
streams of the pool coil.
a) Use full size piping and valve
t
o
c
onnec
t
t
he
“
I
n”
and
“
Out
”
s
t
r
eams
of the pool coil.
b) Allow the boiler to fire contin-
uously for a period of ten (10) to fif-
teen (15) minutes.
c) With the bypass valve wide
open take temperature readings for
the coil.
d) Note: surface temperature
readings taken on a cold day will vary
significantly from test data.
e) Slowly close the bypass valve
and continue to take temperature
readings.
f) Stop when the temperature
di
f
f
er
enc
e
bet
ween
t
he
“
I
n”
and
“
Out
”
streams reaches forty-five (45) to fifty
(50) degrees Fahrenheit.
g) Flowrate should correspond to
six (6) gallons per minute. (See chart
page 7).
(3) Flue Connections:
(A) OTF Series (Outdoor Units)
The OTF heaters are provided with
an outdoor vent cap to be installed
directly on top of the cabinet at the flue
outlet. This vent cap provides for a
waterproof unit as well as proper con-
(B) ITF Series (Indoor Units)
(a) General:
Oil fired units must be connected
to a flue having sufficient draft at all
times to assure proper operation.
(b) Draft:
A draft regulator should be
installed in accordance with the man-
uf
ac
t
ur
er
’
s
i
ns
t
r
uc
t
i
ons
.
Set
t
he
dr
af
t
t
o
a
negat
i
v
e
–.
01
t
o
–.
02
max
.
WC
over the fire.
(c) Roof Clearances:
The flue gas exit of the venting
system should be at least three (3)
feet above the outside point where it
passes through the roof and at least
two (2) feet higher than any portion of
a building within ten (10) feet of the
venting system.
(d) Chimney Connections:
The horizontal length of a chim-
ney connector should not exceed ten
(10) feet unless a draft booster is
used. The connector should be
pitched upward at least one-quarter
(1/4) inch to the foot. Use only high
quality lock seam smoke pipe. Each
joint should be securely fastened with
sheet metal screws. Chimney con-
nections should be positioned to
effect the shortest possible run of
smoke pipe to the chimney.
(e) Vent Cap:
Install a UL listed vent cap where
the possibility of down draft exists.
Section II
Filling
Instructions
The Thermotron Pool Heater is
an indirect heater using primary water
in the boiler shell to act as a heat
transfer medium to the pool water
flowing through the separate all
copper/bronze heat exchanger coil.
Therefore the pool heater, or boiler
section, MUST be filled with fresh city
water. DO NOT FILL WITH CHLO-
RINATED OR WATER FROM THE
SWIMMING POOL.

3
(1) Do not turn on electrical
power to heater until boiler is properly
filled with water.
(2) * Connect the male end of a
garden hose to the hose adapter of
the heater drain valve.
(3) Open the vent at the top of
the boiler section location as shown
on page 4.
(4) Turn on water and open drain
valve, allow water to flow into boiler
section.
(5) When water flows out of
boiler vent, close vent and leave
heater drain valve open until pressure
gauge reads approximately 10 PSI.
(6) Close drain valve and dis-
connect hose.
(7) Pool temperature control
should be set at desired temperature.
(8) Burner can now be operated
as per specified instructions.
*You may choose to install permanent pip-
ing...filling instructions would be the same.
IMPORTANT NOTICE
Winterizing The Heater:
If the pool heater is installed in an
area known to have a freezing climate
it is necessary to COMPLETELY drain
both the primary boiler and indirect
heat exchanger (pool coil).
Connect a hose to the boiler drain
at the bottom of the boiler section.
Open the vent at the top of the boiler,
as well as the drain valve and drain
the
boiler
section
completely.
Disconnect the unions and the piping
at the pool coil heat exchanger.
Remove the 1/8" pipe plugs in the bot-
tom of the pool coil heat exchanger
header (to be completely certain that
all water is out of the indirect heat
exchanger, it may be advisable to
remove the pool coil completely or
force an anti-freeze solution into the
pool coil.)
S e c t i o n I I I
S t a r t U p a n d
O p e r a t i o n
A Start Up:
(1) Make sure the electrical
power is turned off.
(2) Check the Oil Burner ignition
electrodes carefully and adjust if nec-
essary.
(3) Check to be certain oil tank is
full.
(4) Be certain unit is filled with
water as per filling instructions.
(5) Turn on pool filter pump.
(6) Set limit control at 180°.
(7) Install pressure gauge in the
nozzle port of the fuel pump. Do not
take reading at the bleed port. The
pressure gauge should have a mini-
mum range of 100 PSI. Consult Fuel
Pump specification sheet (shipped
with Oil Burner).
(8) Turn on burner power switch.
(9) Push the safety reset button
on the primary control and release.
(10)Bleed the fuel unit on one-
pipe systems as soon as the burner
motor starts. To bleed, attach a piece
of 1/4" OD clear plastic tubing to the
end of the bleed port. Loosen same
and purge oil of air for at least 15 sec-
onds after oil appears to be clear. If oil
stream does not become clear and
free of air bubbles or foam, check all
fittings, filter and valve connections.
Foam can also be caused by kinks in
the oil line, causing an oil vacuum
condition. High vacuum readings can
al
s
o
be
c
aus
ed
by
t
oo
hi
gh
a
“
l
i
f
t
”
or
too small diameter tubing. Consult
Fuel Pump specification sheet.
B Equipment Adjustments:
Equipment Required:
(1) CO
2
Analyzer (absorption
type)
(2) Draft Gauge
(3) Fuel Pressure
Gauge/Vacuum Gauge
(4) Stack Thermometer
(5) Smoke Tester (Bacharach
Type)
Allow the burner to operate continu-
ously for at least 15 minutes and
then make adjustments:
(a) Combustion Samples:
Should be taken through the
observation port above the burner,
directly over the fire.
(b) Draft:
Take a draft reading over the fire
(OTF outdoor equipment will range
f
r
om
“
0”
t
o
–.
01
negat
i
v
e
mi
ni
mum)
.
(ITF indoor equipment should be
adj
us
t
ed
t
o
a
–.
01
dr
af
t
mi
ni
mum
t
o
a
–.
02
max
.
)
(c) Pump Pressure:
Adjust the pump discharge pres-
sure to 100 PSI. Vacuum must not
exceed 6" on one pipe and 10" on a
two-pipe system.
(d) Combustion Settings/CO
2
Reduce the air supply by closing
the air band to allow just sufficient air
for clean combustion. This is accom-
plished by loosening the lock screws
on the air shutter and closing the air
shutter until a TRACE of smoke is
recorded. Take a CO
2
sample, which
should be approximately 12%. Open
the air shutter and lower CO
2
reading
approximately by 1-1/2 to 2% from the
abov
e
r
eadi
ng.
A
“
0”
s
mok
e
r
ead
ing
should result with a CO
2
reading of
approximately 10%.
(e) Stack
Temperature:
(ITF
only)
Check to see that the stack tem-
perature is approximately 500° above
the ambient temperature.
(f) Turn LIMIT CONTROL to the
lowest setting; burner should shut
down. Turn back to the desired set-
ting, (normally 180°) burner should
operate.
(g) Turn POOL TEMPERATURE
CONTROL down to lowest setting;
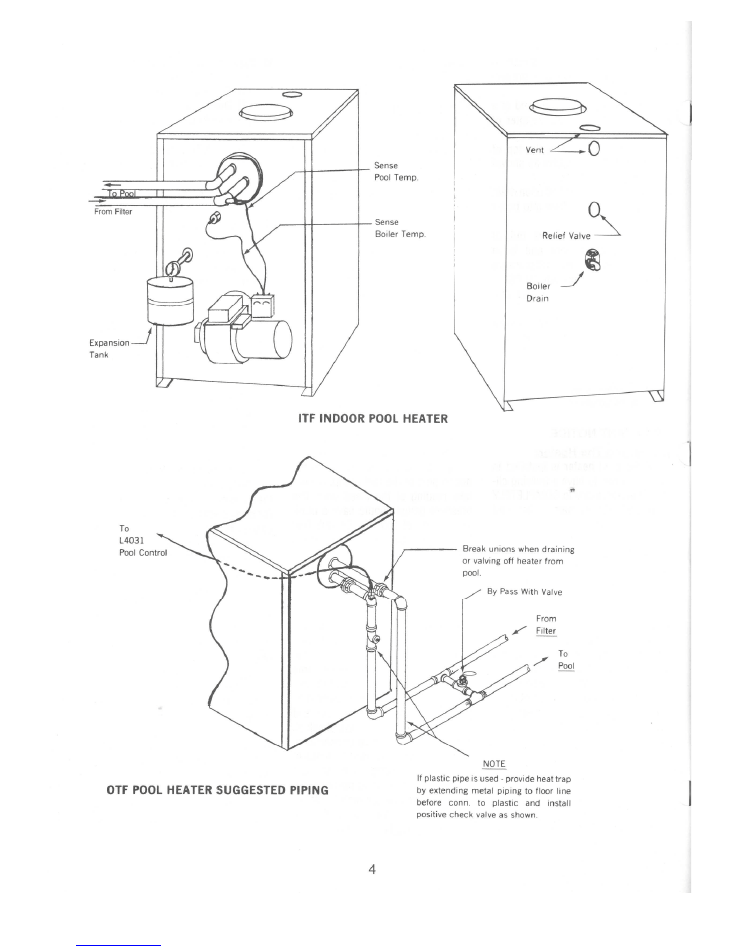

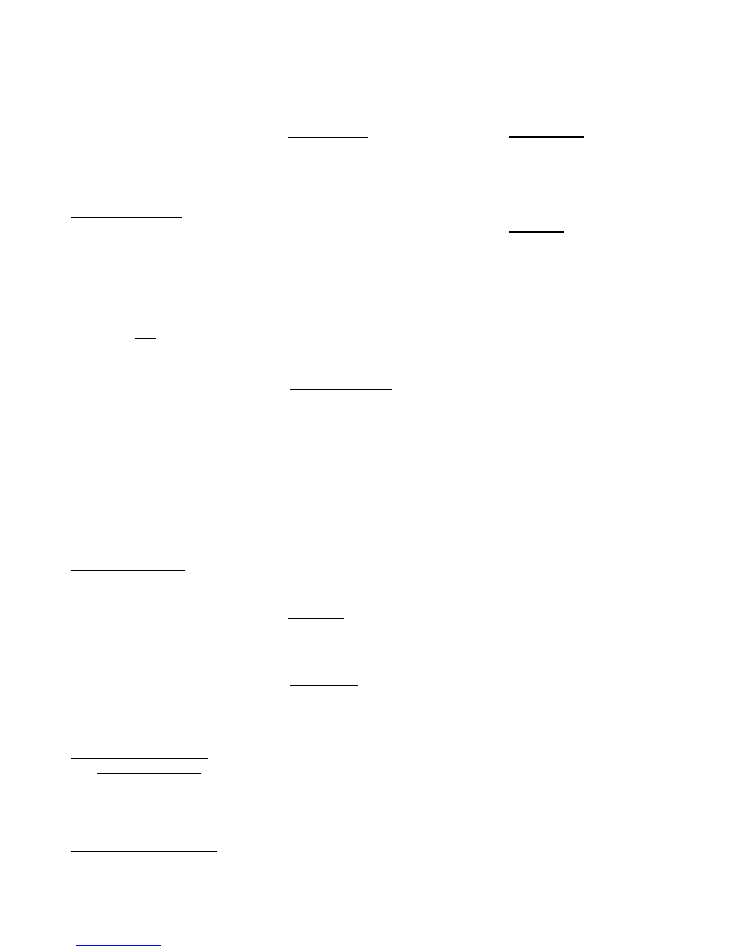
6
burner should shut down. Turn con-
trol to highest setting; burner should
operate. Reset to desired tempera-
ture, approximately 80°.
(h) Allow burner to operate until
pool is at desired temperature. Adjust
pool
t
emper
at
ur
e
c
ont
r
ol
“
c
ool
er
”
unt
i
l
burner shuts down. This is the setting
that will be maintained by the heater.
C Trouble Shooting
(1) Motor Does Not Run:
(a) Check fuses and power to
heater.
(b) Set pool temperature control
and boiler temperature limit
to highest setting.
(c) Reset primary control (push
red button). Reset button
should only be pushed one
time!
(d) Reset thermal overload
button on motor.
(e) Check for defective tempera-
ture controls by jumping the
controls one side at a time.
(f) Check for power to motor. Motor
may be defective.
(g) Ensure that boiler is pressur-
ized with water. The low
water cutoff disrupts the
electrical circuit for the burn-
er.
(2) Motor Runs - No Fire:
(a) No oil in tank.
(b) Bad or plugged burner
nozzle.
(c) Blocked oil line.
(d) Loose transformer connec-
tions/defective ignition
transformer.
(e) Inspect electrode settings
and insulators.
(f) Check fuel pump pressure.
(3) Burner Fired--Shuts Down
On Cad Cell Safety:
(a) Defective C-554 Cad Cell.
(b) Dirty Cad Cell.
(c) Defective R-7184A primary
control.
(4) Smoke Coming Out of Flue:
(a) Clogged nozzle.
(b) Dirty fan/air handling parts.
(c) Improper burner adjustment
refer to B Equipment
Adjustment.
(5) Cycling On/Off:
(a) Differential between pool
setting and high limit too
close.
(b) High limit setting too low.
(c) Remote pool sensing bulb in
outlet water piping instead of
inlet water piping.
S e c t i o n I V
C a r e a n d
M a in te n an c e
(1) Heat Exchanger:
The tubular portions of the heat
exchanger should be cleaned annual-
ly or at start-up each heating season.
(a) Remove the cabinet top.
(b) Remove the flue collector
top.
(c) Remove all baffles from fire
tubes.
(d) Brush clean the flue ways
with a 2" soft brush and vac-
uum the unit carefully.
Reverse the above steps.
(3) Oil Burner:
(a) Thoroughly brush clean the
burner fan blades. Proper
combustion air delivery is
only possible when fan
blades are clean.
(b) Clean nozzle assembly and
all other air handling parts.
(c) Check spacing and condition
of electrodes. Adjust or
replace as necessary.
(d) Nozzles should be inspected
for malfunctions. If nozzle
does not perform according
to the prescribed conditions
under
“
bur
ner
adj
us
t
ment
s
,
”
replace it with only the spec-
ified type.
(4) Lubrication:
For unsealed motor bearings
only, lubricate the motor annually with
two (2) drops of SAE-10 nondetergent
oil.
(5) Gaskets:
Carefully tighten nuts on the pool
heat exchanger flange to prevent gas-
ket leaks. DETERIORATION DUE TO
GASKET LEAKS SHALL VOID THE
WARRANTY.
(2) Oil Filter:
The oil filter cartridge should be
replaced annually.
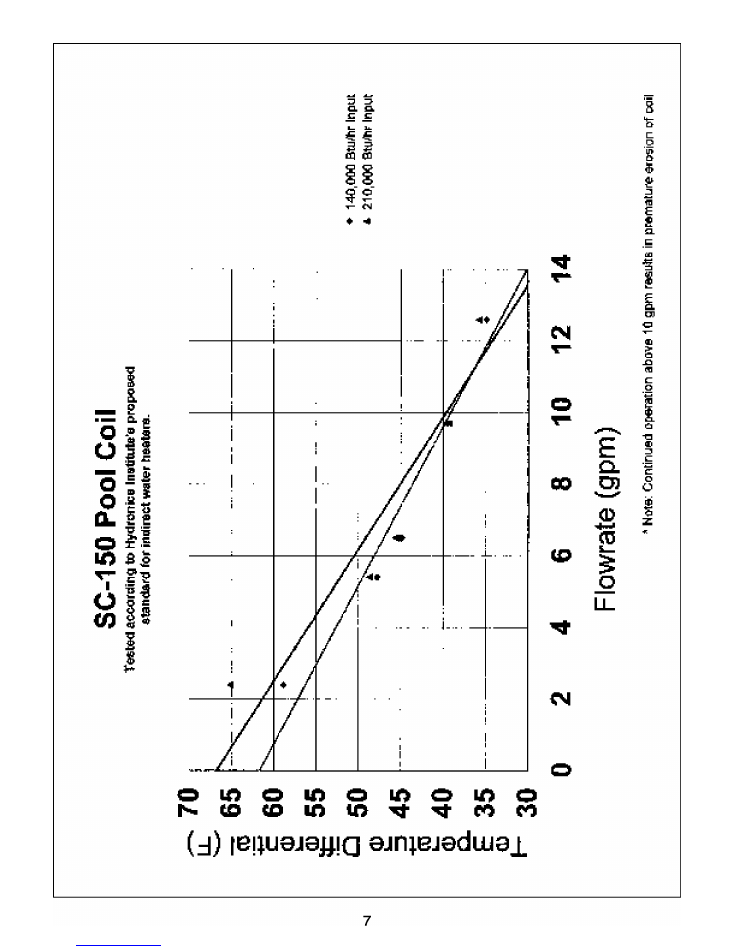
7
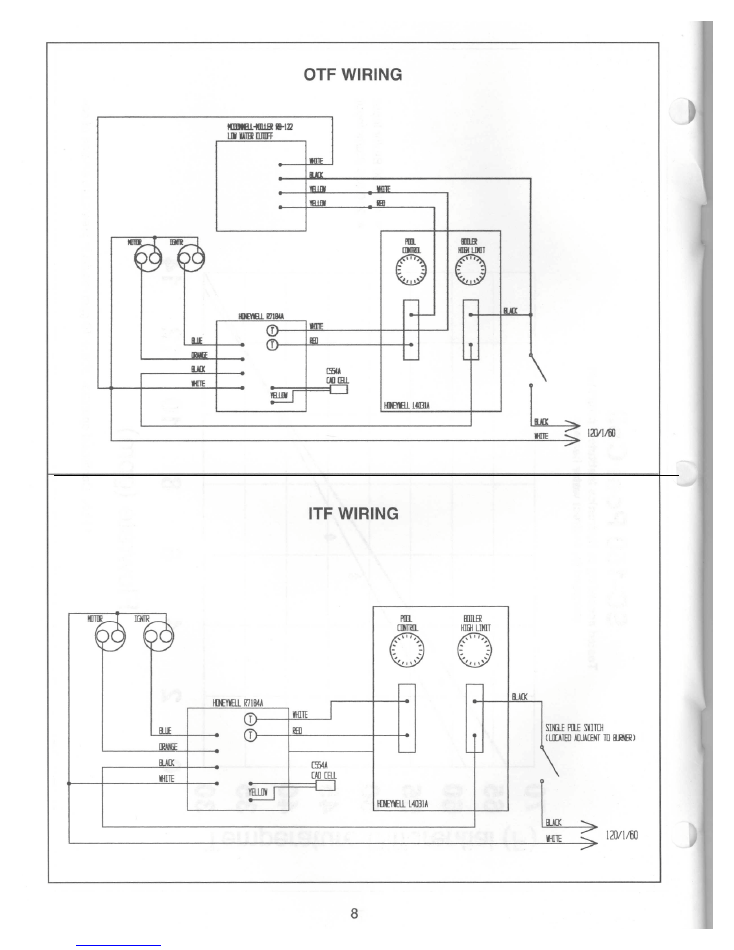

9
P a r t s L i s t
Item No.
OTF/ITF 510/1600 Beckett AF Burner Parts List - #540500
(Designate heater and burner model numbers on all orders.)
Description
Part
Number
1
Motor 1/7 HP 3450 RPM - PSC
675141
2
Fan 4-1/2 Dia. x 3-7/16
675130
3
Flexible Coupling
675160
4
Beckett Single Stage Clean-Cut Fuel Pump
675315
5
France Electronic Igniter
675981
6
Head F-3 (510/560)
675400
6
Head F-12 (640-801)
675420
6
Head F-22 (901-1600)
675430
7
Electrode Assembly
675500
8
Gun Assembly (Nozzle Line/Electrode Assy.)
675630
9
Air Tube Combination Pkg. (510/801)
675620
9
Air Tube Combination Pkg. (901/1600)
675640
10
Burner Flange Gasket
675170
11
Blank Air Band (510/801)
675110
11
8 Hole Air Band (901/1600)
675120
Cad Cell C-554-A
553024
Nozzle 2.50 x 80° Hollow
680246
Primary Control R7184B
553010
Coil Gasket
481000
Pool Controller L4031A
552035
SC-150 Coil (510-801)
530060
Temperature and Altitude Gauge
SC-200 Coil (901-1600)
530070
1/4 - 2-1/2" Round
559560
Ceraform Sleeve
352000
Relief Valve - 3/4"
575020
#15 Expansion Tank (510 thru 801)
972000
Nozzle 1.00 x 80° Hollow
680146
#30 Expansion Tank (901 thru 1600)
972010
Nozzle 1.50 x 80° Hollow
680196
McDonnell Miller Low Water Cutoff
553101
Nozzle 2.00 x 80° Hollow
680226
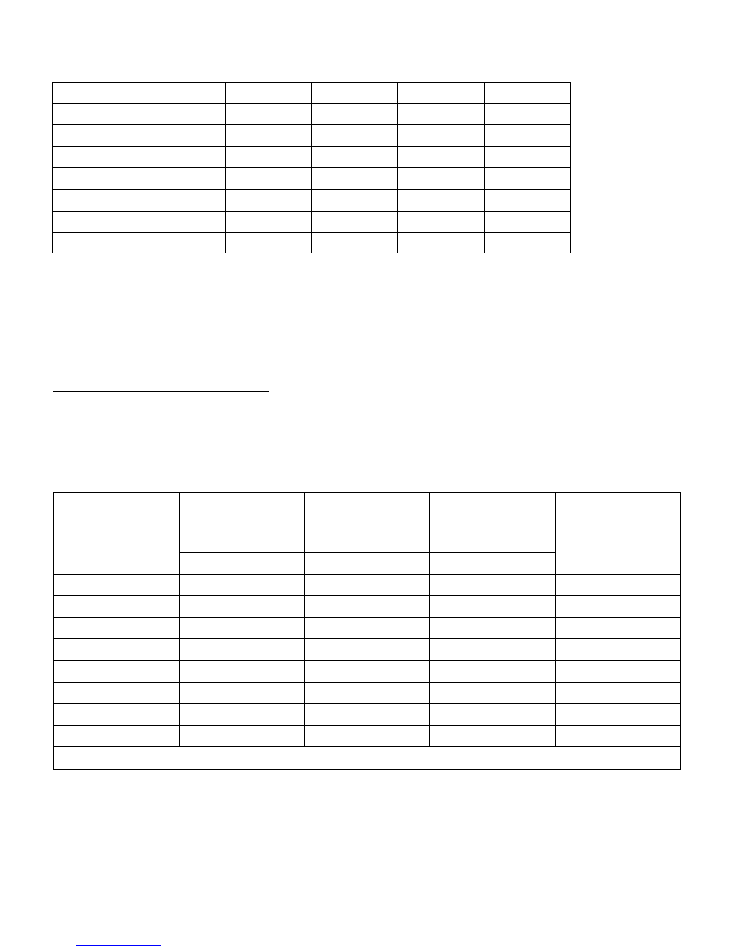
10
Specifications
Model - OTF - ITF
510
801
1010
1600
Gross Input
140,000
210,000
280,000
350,000
Gross Output - BTU/Hr.
109,200
163,800
218,400
273,000
Flue Pipe Dia.
6"
6"
8"
8”
Firing Rate - GPH
1.00
1.50
2.00
2.50
Width OTF-ITF
22"
22"
26-1/4"
26-1/4"
Length OTF-ITF
31"
31"
34"
34"
Height OTF-ITF
38-1/2"
38-1/2"
45"
45"
STANDARD EQUIPMENT
OTF
—
Al
umi
num
j
ac
k
et
wi
t
h
s
el
f
v
ent
i
ng
/
I
TF
-
Fl
us
h
J
ac
k
et
wi
t
h
Bak
ed
Enamel
Fi
ni
s
h
Boiler body with combustion chamber installed, theraltimeter, completely assembled and packaged with oil burner,
cadcell relay, pool & limit control, low water cutoff (OTF only), relief valve, indirect pool heating coil SC-150 (510/801)
SC-200 (1010/1600) with 1-1/2" I.P.S. tappings.
Selection of the right size OTF/ITF Heater
There are many factors related to proper sizing of Pool Heaters. We recommend you contact your installing dealer for
help in determining the correct size for your particular application.
POOL HEATER SIZING CHART - HEAT LOSS FROM POOL SURFACE - BTUs PER HOUR
Desired
PoolTemperature
(°F)
Surface Area of Pool
Sq. Ft.
80°
85°
90°
Approximate
Gallons
500
137,000 Btu.
155,000 Btu.
200,000 Btu.
20,000
600
166,000 Btu.
185,000 Btu.
240,000 Btu.
24,000
700
200,000 Btu.
218,000 Btu.
280,000 Btu.
28,000
800
220,000 Btu.
250,000 Btu.
320,000 Btu.
32,000
900
248,000 Btu.
280,000 Btu.
360,000 Btu.
36,000
1000
275,000 Btu.
310,000 Btu.
400,000 Btu.
40,000
1200
330,000 Btu.
370,000 Btu.
480,000 Btu.
48,000
1400
384,000 Btu.
435,000 Btu.
560,000 Btu.
56,000
1600 or Larger: Refer inquiry to Thermo-Dynamics, Schuylkill Haven, PA 17972
NOTES: 1. These heat losses are based on an assumed wind velocity at the water surface of 5 m.p.h. and an ambient
temperature of 60°F.
2. Where surface area and gallons do not coincide, surface area must take precedence.
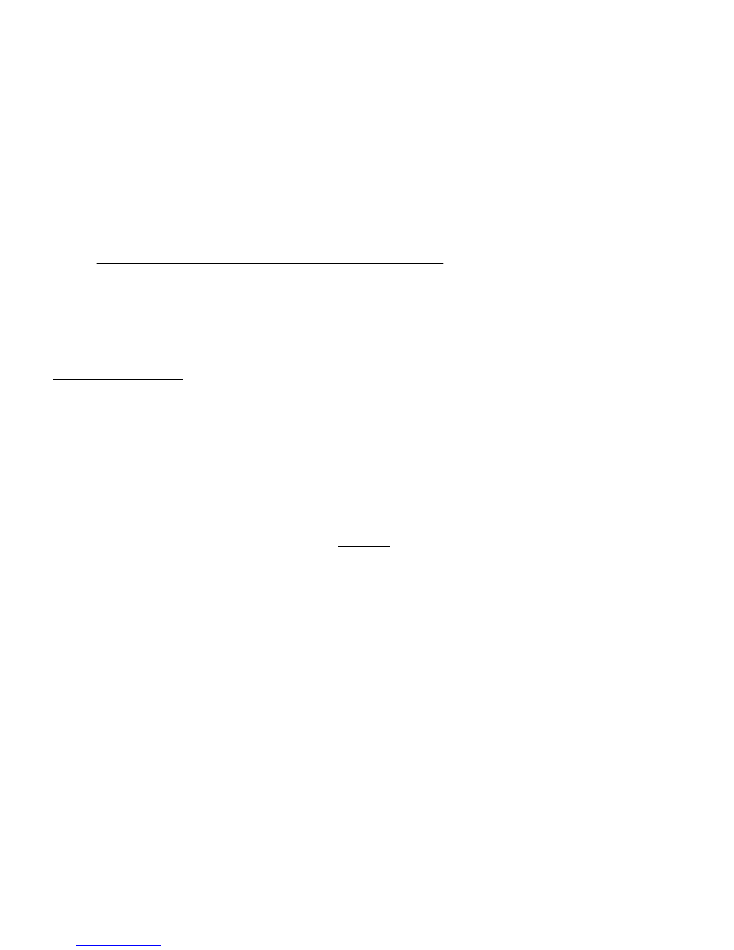
11
H o m e O w n e r I n f o r m a t i o n :
The Service Company:
Name
Address
Phone No.
SERVICE INFORMATION:
To avoid unnecessary expense and inconvenience your pool heater should be cleaned and serviced at least annu-
ally by a qualified service man. If difficulty occurs, the following should be observed before calling a service man:
(a) Check to be sure there is fuel in tank.
(b) Make sure power switch is turned on.
(c) Check to see if the desired pool setting is greater than the temperature of the pool.
WARNING
EVEN THOUGH THE VENT CAP AREA IS APPROXIMATELY 40 INCHES ABOVE GROUND, KEEP SMALL CHILDREN AWAY
FROM YOUR POOL HEATER.
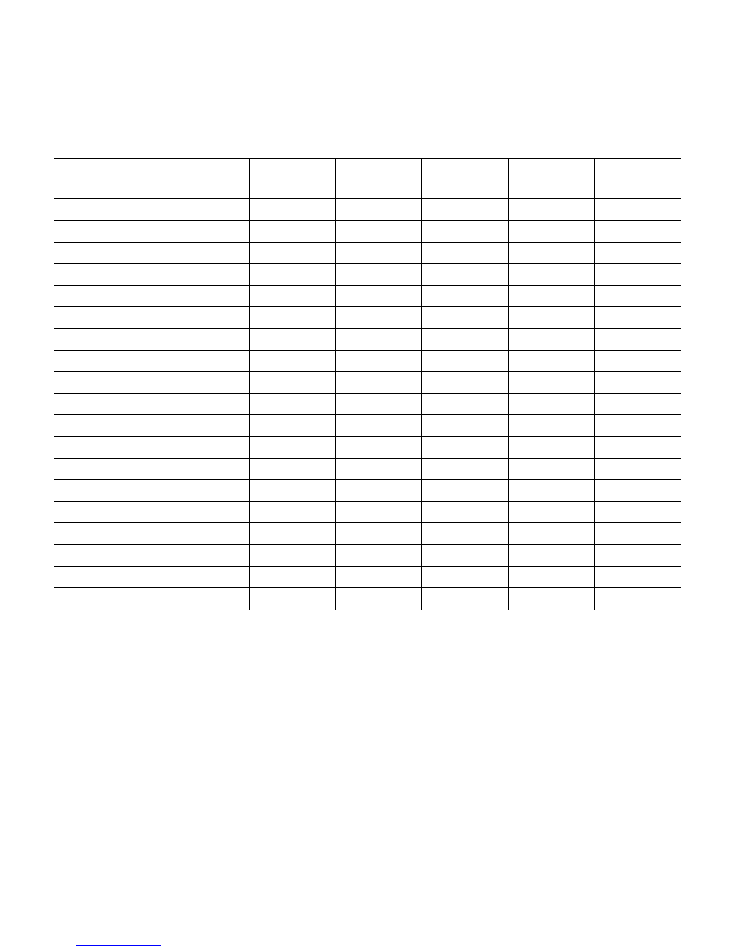
12
OTF/ITF Pool Heater
Beckett AF Burner
Service Set Up Records
I
nitial Set Up
1
2
3
4
1. Date
2. Model Number
3. Firing Rate
4. Pump Pressure
5. CO
2
6.
“
0”
Smok
e
7. Gross Stack
8. Draft Over Fire
9. Replaced Filter Yes/No
10. Replaced Nozzle Yes/No
11. Clean Pump Filter Yes/No
12. Inspect Coil Gasket
13. Check for Leaks @ Plugs/Fittings
14. Brush Clean Flue Tube Passages
15. Vacuum Chamber/Flue Tubes
16. Clean Blower Wheel
17. Check/Set Electrodes
Swimming Pool Heater Warranty
( 5 - Y e ar L i m i t e d )
Swimming Pool Heaters (boiler wet section) are guaranteed for 5 years against defective material and work-
manship from the date of installation. The indirect heat exchanger (copper pool coil) are guaranteed for 1 year
against defective material and workmanship from the date of installation. Controls and accessories made by
others and attached to or furnished with the Swimming Pool Heaters are guaranteed (only) to the extent of the
manuf
ac
t
ur
er
’
s
guar
ant
eed.
Thi
s
war
r
ant
y
i
s
s
epar
at
e
f
r
om
t
he
Ther
mo-
Dy
nami
c
’
s
r
es
i
dent
i
al
war
r
ant
y
.

Part Number 595821
250 - 6/03
MIP-6426