Full Text Searchable PDF User Manual
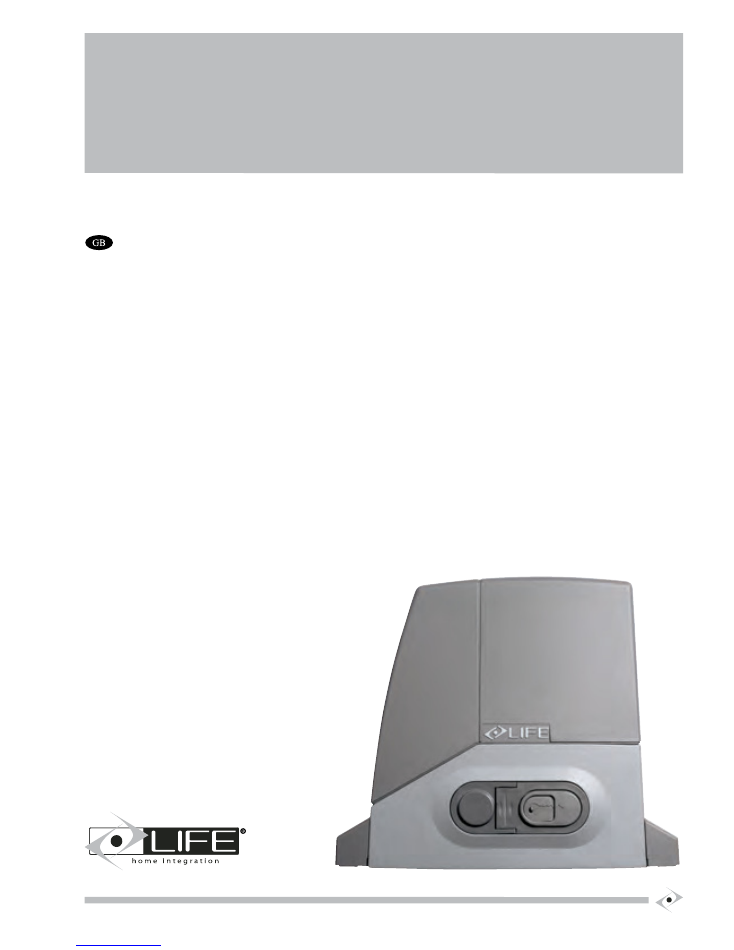
ACER
VERSIONE 10/2007
AUTOMAZIONE PER CANCELLO SCORREVOLE
ISTRUZIONI E AVVERTENZE PER L`INSTALLAZIONE,E L`USO E LA MANUTENZIONE
ELECTROMECHANICAL OPERATOR FOR SLIDING GATES
INSTRUCTIONS FOR INSTALLATION, USE AND MAINTENANCE
MOTOREDUCTEUR ELECTROMECANIQUE POUR PORTAILS COULISSANTS
INSTRUCTIONS POUR L’INSTALLATION, L’UTILISATION ET L’ENTRETIEN
MOTORREDUCTOR ELECTROMECÁNICO PARA CANCELAS CORREDERAS
INSTRUCCIONES PARA LA INSTALACIÓN, EL USO Y EL MANTENIMIENTO
MOTORREDUCTOR ELECTROMECÂNICO PARA PORTÕES DE CORRER
INSTRUÇÕES PARA A INSTALAÇÃO, USO E MANUTENÇÃO
ELEKTROMECHANISCHER SCHIEBETORANTRIEB
ANLEITUNGEN UND HINWEISE FÜR INSTALLATION, GEBRAUCH UND WARTUNG
MOTOREDUKTOR ELEKTROMECHANICZNY DO BRAM PRZESUWANYCH
INSTRUKCJA MONTAŻU, UŻYTKOWANIA I KONSERWACJI
ЭЛЕКТРОМЕХАНИЧЕСКИЙ РЕДУКТОРНЫЙ МОТОР ДЛЯ РАЗДВИЖНЫХ ВОРОТ
ИНСТРУКЦИЯ ПО МОНТАЖУ, ИСПОЛЬЗОВАНИЮ И ТЕХНИЧЕСКОМУ ОБСЛУЖИВАНИЮ
ELEKTROMECHANICKÝ POHON PRE POSUVNÉ BRÁNY
NÁVOD NA INŠTALÁCIU, POUŽITIE A ÚDRŽBU
ELEKTROMECHANICKÝ POHON PRO POSUVNÉ BRÁNY
NÁVOD NA INSTALACI, UŽÍVÁNÍ A ÚDRŽBU
ELEKTROMECHANIKUS MOTOR TOLÓKAPUKHOZ
UTASÍTÁSUK ÉS FIGYELMEZTETÉSEK TELEPÍTÉSHEZ, HASZNÁLATHOZ ÉS KARBANTARTÁSHOZ
V.1
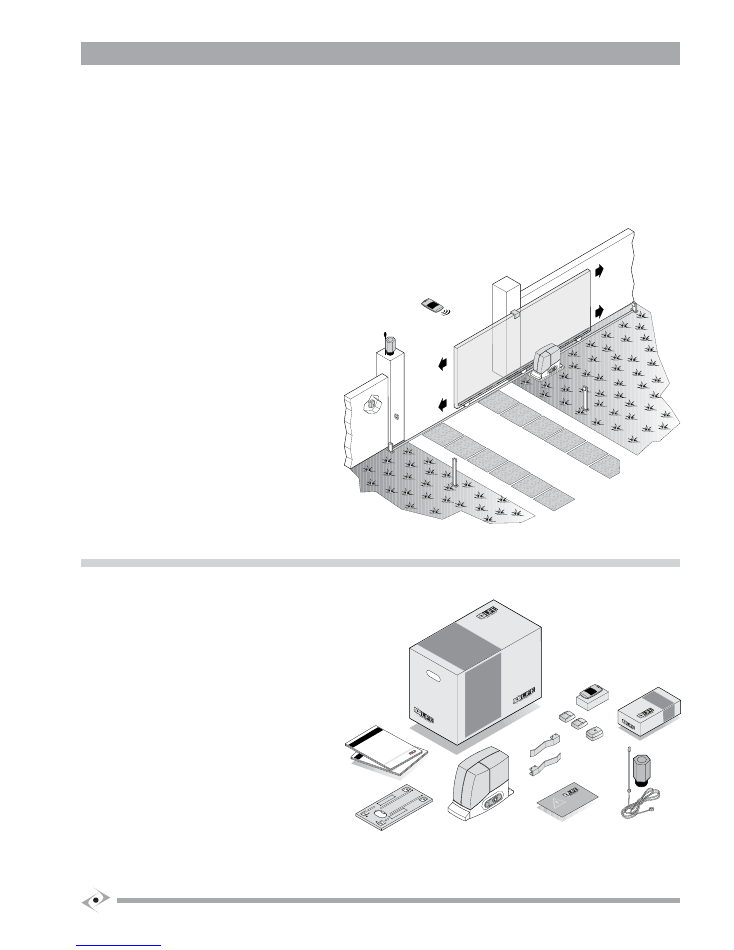
STANDARD INSTALLATION
Fig.1:
componenti e dispositivi di un’automazione tipo.
Fig.1:
components and devices of a typical automation.
Fig.1:
composants et dispositifs d’un automatisme type.
Fig.1:
componentes y dispositivos de un automatismo tipo.
Fig.1:
componentes e dispositivos de uma automação tipo.
Abb.1:
Bestandteile und Vorrichtungen eines Musteranstriebs, siehe Abbildung.
Obr.1:
części i urządzenia typowego siłownika.
Рис.1:
детали и устройства для оборудования типа см. рис.
Obr. 1:
Súčiastky a zariadenia typickej inštalácie, pozri obrázok.
Obr. 1:
Součástky a zařízení typické instalace, viz obrázek
Tab.1:
általános automatikához tartozó robbantott rajz, lásd ábra.
Tab. 2:
descrizione contenuto scatola attuatore ACER.
Fig.2:
description of the contents of the ACER pack.
Fig.2:
description contenu boîtier ACER.
Fig.2:
descripción del contenido de la caja ACER.
Fig.2:
descrição do conteúdo da caixa ACER.
Abb.2:
Beschreibung des Verpackungsinhalts ACER, siehe Abbildung.
Obr.2:
opis zawartości opakowania ACER.
Рис.2:
Описание содержимого коробки ACER.
Obr. 2:
Popis obsahu škatule ACER, pozri obrázok.
Obr. 2:
Popis obsahu balení ACER, viz obrázek
Tab. 2:
ACER szetthez tartozó doboz tartalma, lásd ábra.
AC001
RE
CA
inoiz
urtsi
idela
una
M
RE
CA
inoi
zurt
sii
del
aun
aM
GN
INE
PO
RO
OD
CIT
AM
OT
UA
R
E
C
A
1 A
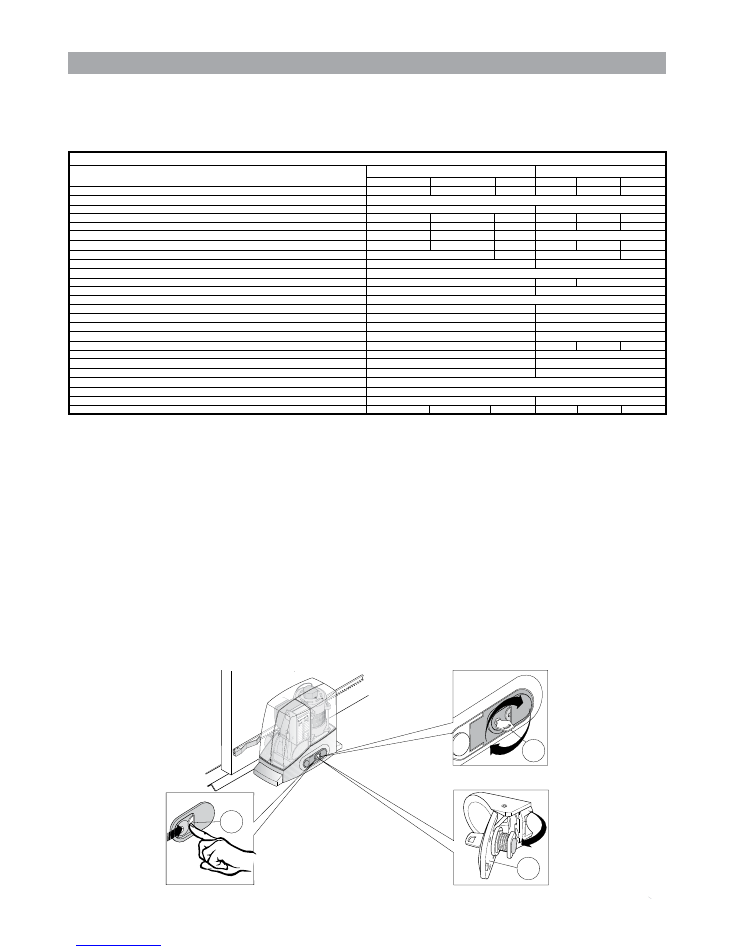
H
SI
L
G
N
E
TECHNICAL FEATURES
LIFE home integration
reserves the right to make changes to technical characteristics at any time and without prior notice, without changing its intended
use and function.
ACER
: Irreversible electromechanical operator for sliding gates with optical/magnetic encoder and built-in ECU
Version:
ECU – 230 V ac 50 Hz
ECU – 24 V dc
AC4 / AC4R AC6 / AC6R AC8 AC4 24 P AC6 24 X AC8 24 X
Built-in ECU
RG1A / RG1R RG1A / RG1R RG1A RG1 24 P RG1A 24 X RG1A 24 X
Power supply
V
230 Vac 50 Hz
Motor power supply
V
230 V a.c. 24 V d.c.
Motor power
W
250 280
300
40
80
90
Power input from mains 230V / Max. motor absorption at pick-up 24 V A
1,1 1,2
1,4
5
6
12
Capacitor
µF 14 14
16
NO
Thrust
N
500 700
900
300
500
700
Lubrication
Tipo grease
oil
grease
oil
Thermal protection device °C
140
NO
Limit switch
2 electromechanical or magnetic limit switches in M version
Encoder
optical
magnetic
optical
Speed
m/min 10
11
External toothed wheel module
4
Number of teeth external toothed wheel
20 16
Work cycle
%
35 80
Nominal work time
min
10 20
Battery recharge time (optional)*
BATTERY NOT PROVIDED 48
Opening cycles with charged battery*
BATTERY NOT PROVIDED 20
15
10
Operating temperature °C
from -20 a +70
Protection class
IP
54
Motor insulation class
F D
Assembly
horizontal with dedicated anchorage plate
Dimensions / weight
170 (plate) x 342 x 288 (h) mm / 10 kg
Use in acid, saline or potentially explosive environment
no
Max gate weight
kg
400 600
800
400
600
800
* for 2 Ah batteries (optional and installed in control unit).
1.0 INSTALLATION
1.1
Operator release
Attention:
• The fitter must permanently fix the label describing the manual release operation close to the manual release key.
• T
he activation of the manual release could cause an uncontrolled movement of the gate in the event of mechanical damage or unbalanced conditions.
• Before performing the manoeuvre switch off the electricity supply to the automation.
• To avoid breaking the key,
do
not apply excessive force.
a) Slide the lock protection cover
(1)
. See
fig. (1.1)
.
b) Insert the key
(2)
in the lock and turn to the right through 90°.See
fig. (1.2)
.
c) Gently pull the key outwards until
the hatch is protruding, then pull outwards until it stops. See fig.
(1.3)
.
d) T
he operator is now free and can be moved by hand. A microswitch assembled on the blockage device prevents the motor from operating when
the power comes back on.
e) To reconnect the transmission, turn the opposite way and move the gate manually until it hitches up.
Figur
e
(1)
AC017
3
2
1
Fig.1.2
Fig.1.1
Fig.1.3
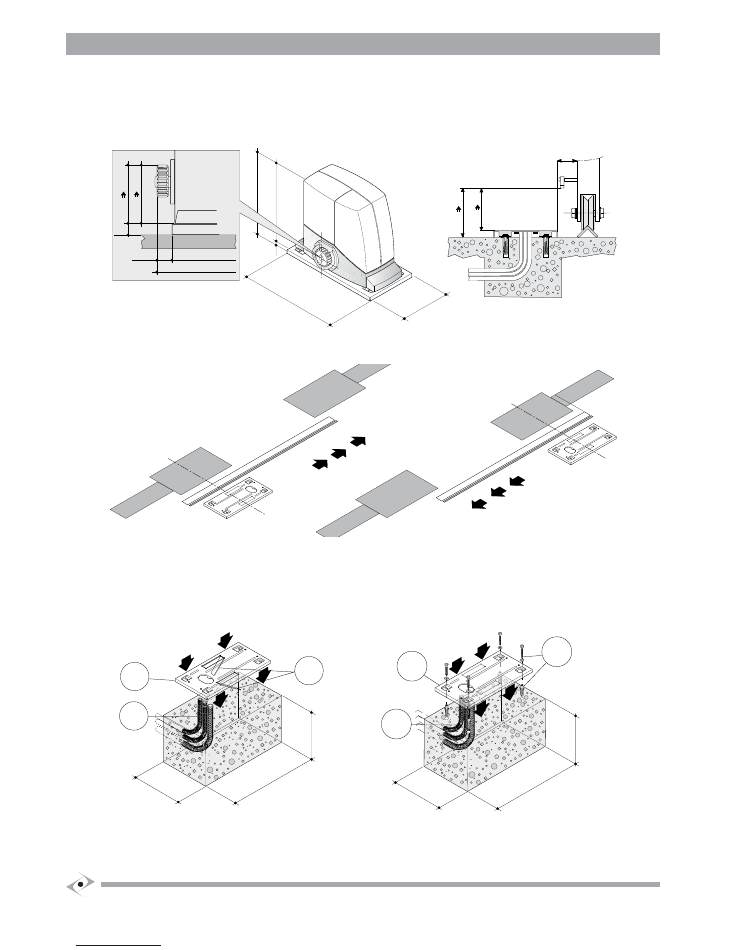
1.2
Installing operator components: positioning and installation of the anchorage plate
The area in which the operator is installed must provide adequate space for performing maintenance and manual release operations.
a)
Adhere to the dimensions in
fig.2
.
Fig. (2)
335
51
170
58
2
00
3
22
170
192
59
61
z
99
81
z
15
AC003a
88
61
z
19
81
z
38
Fig. (3)
b) Observe the orientation in
fig. (3)
for positioning the operator anchorage plate (R – L).
c) Refer to
fig. (2.2)
for the respective heights for 16 or 18-tooth pinions.
d) Lay the electric cable pipes
(4)
, allowing them to protrude and plugging them to prevent them from
filling
with debris.
Fasten the anchorage plate
(1)
to the concrete base with 4 expanding screw anchors
(2)
, see
fig.(4.
2
)
; or sink in the fresh concrete folding the two
“L”s
(3)
, see
fig.(4.
1
)
.
Fig. (4)
1
4
350
250
200
3
AC005
2
1
AC010
4
350
250
200
AC010
35
Fig.4.1
Fig.4.2
ATTENTION: If the operator is subject to heavy work conditions or if the weight of the leaf is over 300 kg, the anchorage plate (1) must be sunk
into the concrete.
Left Hand
Right Hand
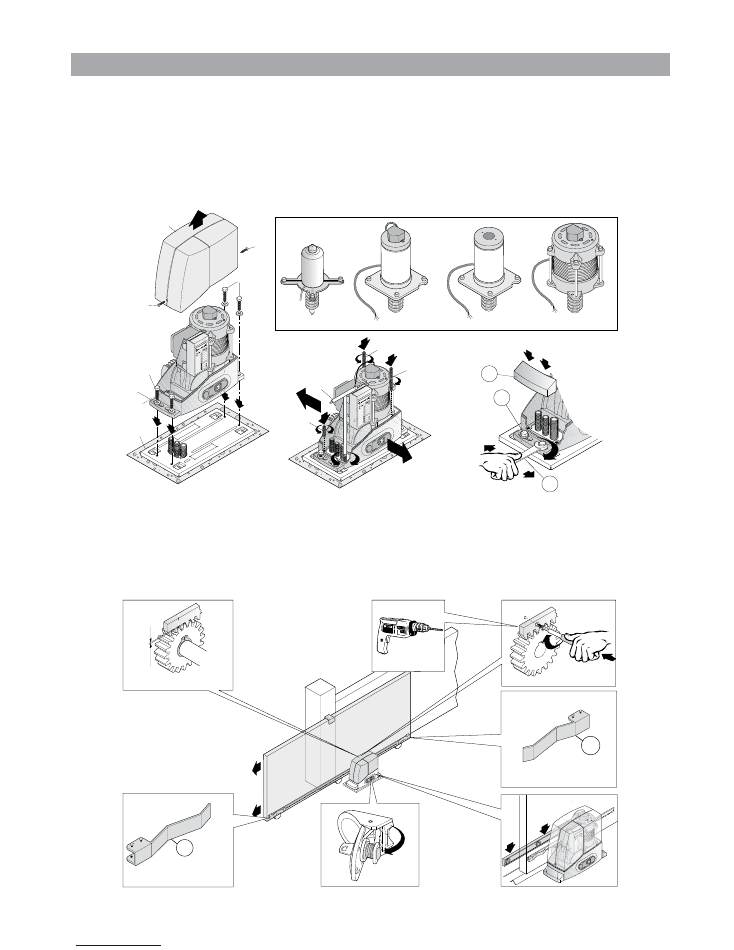
H
SI
L
G
N
E
2
1.3
Installing operator components: positioning and installation of the operator
a) Remove the lid
(2)
of the operator by loosening the screws
(1)
; rest the operator on the anchorage plate and manually turn the 4 M10 screws
(7)
with
the relative washers through 3/4 of a revolution. See
fig. (5.1)
.
b) Vertically adjust the operator using the 4 dowels
(8)
levelling it with the spanner
(9)
; adjust the operator so that it is parallel to the gate. See
fig. (5.2)
.
c) D
efinitively
fasten
the
operator
by
blocking
the
4 M10
screws
(7)
and
the
relative
washers
with
a
fixed
or
tube
wrench
(10)
. Assemble the covers
on the clamping feet
(4)
. See
fig.(5.3)
.
Fig. (5)
AC037
AC4 24P
AC6 24
AC8 24
AC4-AC6-AC8
AC012
7
7
AC012
6
5
7
1
2
1
8
8
8
9
8
AC013
10
7
&
&
4
Fig.5.1
Fig.5.2
Fig.5.3
1.4
Installing operator components: rack assembly
Assemble the “gate open”
(A)
and “gate closed”
(B)
limit switch brackets at the ends of the rack, fastening them with the screws provided in the pack
as indicated in
fig. (6)
. Remember
that
the
gate
will
travel
2-3
cm
more,
after
the
intervention
of
the
limit
switch,
consequently
adjust
the
position
of
the brackets so that the gate does not collide with the mechanical stop plates.
Fig. (6)
B
m
m
1
A
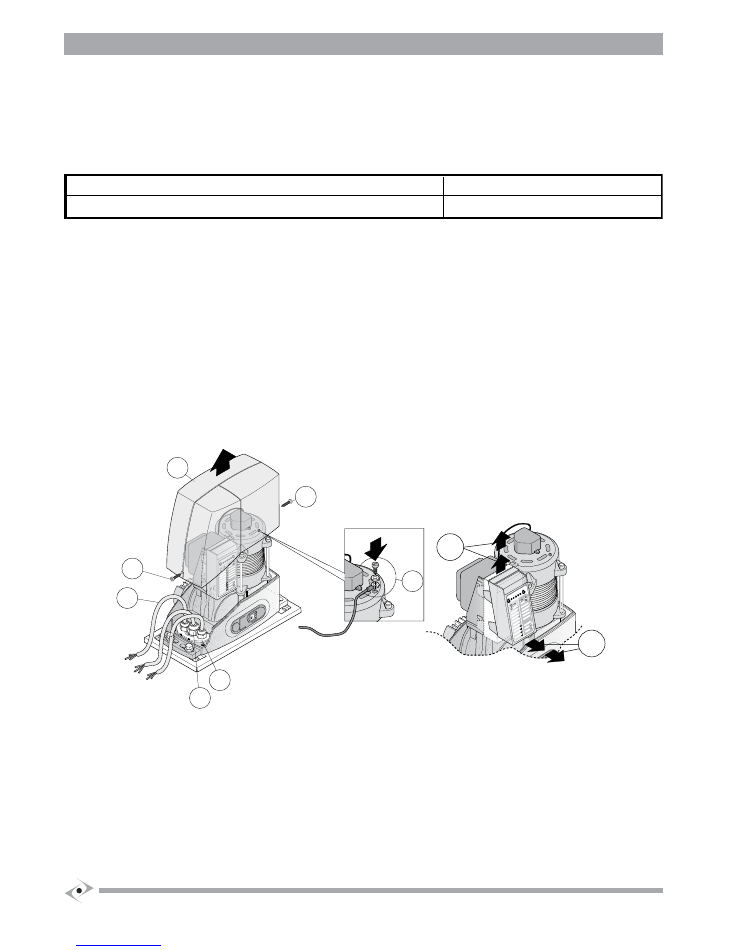
2.0 WIRING AND CONNECTIONS
• The operator must be connected to the relative Life
electronic control unit (ECU)
.
• All wiring and connection operations must be carried out with the control unit disconnected from the electricity supply. If the disconnection device
is not in view, display a sign reading: “ATTENTION: MAINTENANCE WORK IN PROGRESS”.
The internal linear electromechanical operator wiring performed by the Manufacturer, may not be modified under any circumstances.
2.1
Electric connections
Connection
Type of cable
Electricity supply line
3x1,5 mm
2
cable
ATTENTION: the cables used must be suited to the type of installation. It is the Fitter’s responsibility to choose appropriate material.
• The power cable may be
no
lighter than
60245
IEC
57
(
HO5RN-F).
• Inside the power cable, one wire must be yellow and green.
• The power cable coating must be composed of a polychloroprene sheath.
• A
ll wires must be unsheathed as little as possible (6mm at the most) and as close as possible to the connection terminals, in order to prevent accidental
contact with live parts in the event that cables disconnect from the terminals.
• Do not pre-seal cables to be fastened to the terminals using screws.
• A
power cable-fastening device must be provided. Assemble the power cable so that if it comes out of its fastening device, the neutral and live
wires are taut before the earth wire.
2.2
Introducing the electric wires into the operator
a) To access the ECU remove the cover
(2)
of the reduction gear removing the two lateral clamping screws
(1)
.
b) Open the pre-punched holes in the cable gland door
(3)
, insert the cable glands
(17)
, then insert the cables
(18)
needed for the connections (keep
230 V and very low voltage cables separate). Leave the cables about 40cm longer
c) Assemble the cable gland door making it stick well to the edges of the seat in the operator base to prevent access to insects and dirt. See
fig. (7)
.
Fig. (7)
AC021
2
&
&
1
AC020
2
1
&
&
2
&
&
1
18
17
4
3
Fig.7.1
Fig.7.2
2.3
Electronic control unit connections
Fitters must make the connections of the
230
Vac
50
Hz
electricity supply, and the various automation devices. Connections between the ECU, motor,
encoder and autotransformer have already been performed by the Manufacturer.
ATTENTION: for safety reasons, it is essential to earth the motor.
Crimp the yellow and green wire on the power cable to the loop on the upper sleeve, at the point marked by the earth symbol as indicated in
fig. (7.1)
.
To facilitate ECU connection operations and programming, it can be removed from its housing. The operation is straightforward and does not require the
use of any tools:
a) remove the ECU by pulling upwards and, compatibly with the length of the cables, rest
on
the edge of the operator base or hold.
Once the wiring and/or programming work is complete, place the control unit back in its recess by pressing lightly until the 4 clips snap in. See
fig. (7.2)
.
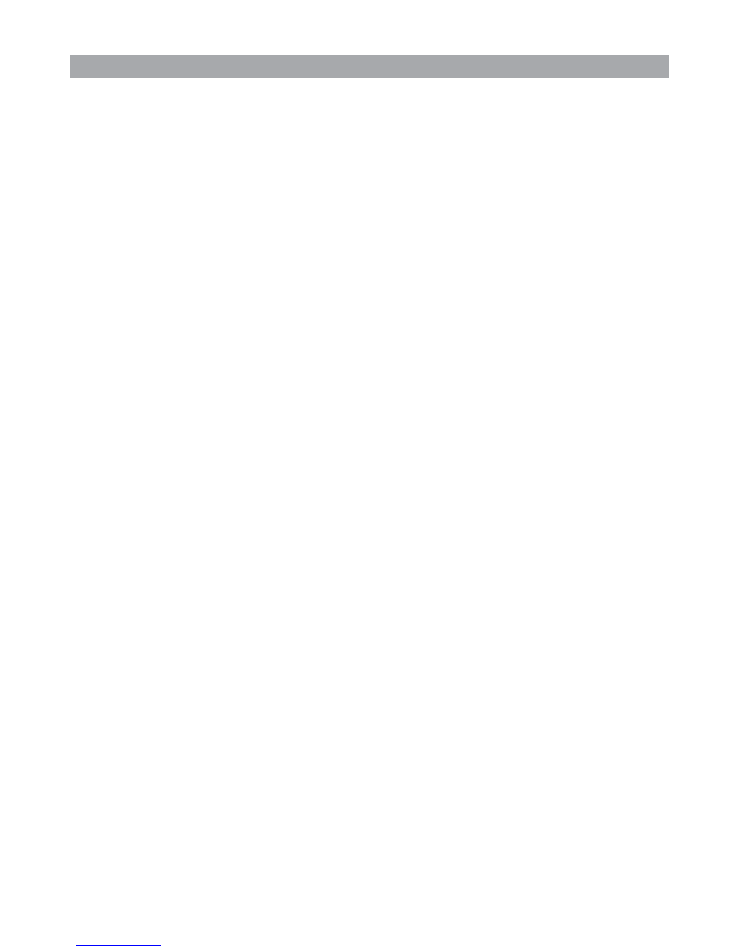
H
SI
L
G
N
E
5
GENERAL INFORMATION
It is strictly forbidden to copy or reproduce this instruction manual without written permission to do so by
LIFE home integration
and will be subject to
verification.
Translation into other languages of all
or part of the manual is strictly forbidden without previous written authorisation from
LIFE home integration
and will be subject to
verification.
All rights on this document are
reserved.
LIFE home integratio
will not accept responsibility for damage or malfunctions caused by incorrect installation or improper use of products and Users are therefore recommended to read this manual
carefully.
LIFE home integration
will not accept responsibility for damage or malfunctions caused by the use of the operator together with the devices of other manufacturers; such action will render the warranty void
LIFE home integration
will not accept responsibility for damage or injury caused by non-compliance with the installation, set up, maintenance and use indications contained in this manual and the safety instructions described
in the SAFETY INSTRUCTIONS AND WARNINGS
chapter.
With the aim of improving its products,
LIFE home integration
reserves the right to bring about alterations to them at any time, without giving
prior
notice.
This document conforms to the state of the automation at which it is provided when released for
sale.
INFORMATION ON THE MANUFACTURER
LIFE home integration
is the manufacturer of the
ACER
operator (and will hereinafter be referred to as manufacturer) and the owner of all rights concerning this
document.
The Manufacturer’s information
required by Machinery Directive 98/37/EC is given below:
•
Manufacturer:
LIFE home integration
•
Address:
Via I Maggio, 37 – 31043 FONTANELLE (TV) Italia
•
Telephone:
+ 39 0422 809 254
•
Fax:
+ 39 0422 809 250
•
http:
www.homelife.it
•
e-mail:
info@homelife.it
The identity plate bearing the information on the Manufacturer of the operator is
fixed
to the control
unit.
The plate
specifies
the type anddate (month/year) of manufacture of the
automation.
For further information on technical or commercial issues and technician call-out and spares requests, Clients may contact the Manufacturer or area representative from which the product was
purchased.
INTENDED USE
•
ACER operators are designed for opening and closing residential-type sliding gates only. Improper use or use on gates larger than those indicated in the TECHNICAL DATA chapter will
be considered non-conform to the intended use. The Manufacturer declines all responsibility for improper use. The owner accepts full responsibility for improper use, which will result
in the warranty being rendered void.
•
Any usage differing from that described above is forbidden.
•
The operator may not be installed or used in potentially explosive environments.
•
The Fitter must ensure that the environment in which the automation is installed is conform to the operator’s temperature range (see Technical Data chap.).
•
The operator is not suitable for use on gates with built-in doors unless the automation is prevented from functioning when the door is open.
• Motorised
gates must conform to current European standards and Directives, including EN 12604 and EN
12605.
• T
he operator may only be used when in perfect working order and in compliance with the intended use, in the awareness of safety and hazard conditions and in observance with the instructions for installation and
use.
• Any
dysfunctions that may pose threats to safety must be eliminated
immediately.
• The
gate must be stable, properly hung and resistant to
flexion
(it must not bend during opening and closure
movements).
• The
operator cannot compensate for faulty or incorrectly hung
gates.
• The
operator may not be used in environments prone to
flooding
• Do
not use the operator in environmental conditions characterised by harsh atmospheric agents
(e.g.
Salty
air).
SAFETY INSTRUCTIONS AND WARNINGS
•
These general rules must always be respected during the installation, connection, testing, trial run, use and maintenance of the automation.
•
The Manufacturer declines responsibility for damage or injury caused by non-conformity with the information supplied concerning installation, trial run, use and maintenance contained
in this manual, and the failure to observe the safety instructions given below.
•
The installation, connection, testing, trial run and maintenance of the operator must be performed by a COMPETENT PERSON aided and supervised by a PROFESSIONAL FITTER.
•
Given the technical, procedural, regulation and legal implications of the work, unauthorised fitters are not permitted.
•
Installation requires a practical and theoretical knowledge of mechanics, electronics and electrics, and of sector laws and standards.
•
Amateur installation is strictly forbidden as it does not comply with current standards and laws and therefore does not guarantee the safe operation of the automation.
•
Do not proceed with installation, connection and trial run in the event of doubts or indecision of any kind.
•
This manual must be read carefully and understood before installing the operator. If doubts arise during installation, contact a PROFESSIONAL FITTER or the MANUFACTURER.
•
Do not perform adjustments and/or parameter memorisation before installation is complete and only if you have understood the procedures described in this manual.
•
Only mount the operator on gates that are perfectly aligned with the sliding tracks and are properly hung. A gate that is not correctly aligned or hung can cause serious injury and/or damage to the operator.
•
The Manufacturer declines all responsibility for damage and faults to the operator caused by non-observance of the instructions contained in this
manual.
• Keep
this manual in a safe and easily accessible place so that it can be consulted rapidly when
necessary.
• During
installation, connection, trial run and usage of the operator, observe all applicable accident prevention and safety
regulations.
• In
the interests of safety and optimal functioning of the operator, only use original spares, accessories, devices and fastening
apparatus.
• D
o not perform alterations on any operator device or
component.
This type of operation may cause
malfunctions.
The Manufacturer declines all responsibility for damage caused by products that have been
modified.
• The
operator should not be used until the setting up procedure described in the STARTING UP chapter has been
performed.
• S
hould liquids penetrate inside the operator, disconnect the electricity supply and contact the Manufacturer’s Assistance Service immediately; use of the operator in such conditions may cause hazard
situations.
• In
the case of faults or problems that cannot be resolved using the information contained in this manual, contact the Manufacturer’s assistance
service.
Storage instructions and warnings
•
The manufacturer declines all responsibility for damage and faults to operator functioning caused by non-compliance with the storage instructions given below.
• The
operator must be stored in closed, dry places, at room temperatures of between –20 and
+70°C.
• Keep
the operator away from sources of heat and naked
flames,
which could damage it and cause malfunctions,
fires
or hazard
situations.
• Keep
the operator in a horizontal position, but not resting on the
ground.
Indications and warnings for use
•
It is the fitter’s duty to perform risk analysis and inform the user/owner of any existing residual risks. Any residual risk detected must be recorded in writing in this manual.
•
The following residual risks are usually present in moving gates: impact and crushing against the main closure surface; impact and crushing in the opening area; shearing between sliding
leaf and fixed part of the track and support during movement; mechanical risks caused by movement.
•
The Manufacturer will not accept responsibility for damage or injury caused by the non-observance of the information on use contained in this manual, and the failure to observe the safety
indications given below.
•
The Manufacturer declines responsibility for damage and malfunctions caused by non-compliance with the instructions for use.
•
Keep this manual in a safe, easily accessible place, so that it can be consulted rapidly when necessary.
• Never
touch the gate or moving parts when they are in
motion.
• Remain
at a safe distance when the gate is in motion: only pass when the gate is completely open and
immobile.
• Prevent
children from playing or standing in the vicinity of the gate or the control organs (radio control), the same precautions should be adopted for disabled persons and
animals.
• In
the event of malfunctions (noisiness, jerky movements,
etc.)
suspend the use of the automation immediately: failure to observe this rule may entail serious hazards, risks of accidents and/or serious
damage to the gate and the
automation.
Contact a PROFESSIONAL FITTER and in the meantime use the gate manually by disconnecting the operator (see the OPERATOR RELEASE
chapter).
• In
order to maintain the operator in
efficient
conditions, ensure that the operations indicated in the MAINTENANCE chapter are performed at the frequency indicated by a PROFESSIONAL
FITTER.
• S
hould liquids penetrate inside the operator, disconnect the power supply immediately and contact the Manufacturer’s Assistance Service; the use of the operator in such conditions may cause hazard
situations.
• If
a problem arises that cannot be resolved using the information contained in this manual, contact the Manufacturer’s assistance
service.
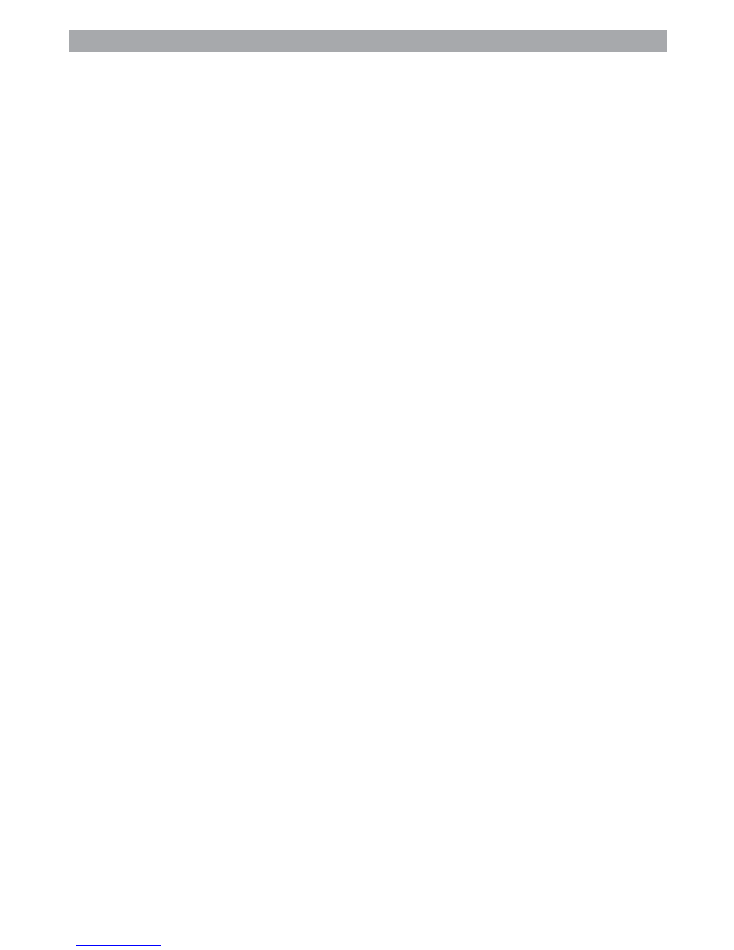
6
Instructions and warnings for installation
•
Before commencing installation read the SAFETY INSTRUCTIONS AND WARNINGS chapter carefully.
•
The person who installs the operator is responsible for performing risk analysis and regulating the automation’s safety devices consequentially.
•
Before commencing installation, check whether further devices or materials are needed to complete the automation in order to suit the specific situation in which it will be used.
• It
is
strictly forbidden to motorise
a
gate that
is
not already efficient and secure
as
the automation cannot resolve faults caused by incorrect installation or poor maintenance
of
the gate.
• During installation, make constant reference to harmonised standards
EN
12453
and EN12445.
• Ensure that the individual devices to be installed are suitable for the automation that one intends to create, paying careful attention to the points raised in the TECHNICAL DATA chapter. Do not proceed
if even just one device is unsuitable for the intended use.
• Ensure that the place
of
installation
is
not prone to flooding, does not contain sources
of
heat or naked flames, fires or hazard situations in general.
• During installation, protect automation components to prevent liquids (e.g. rain) and/or foreign bodies (earth, gravel, etc) penetrating inside.
Preliminary checks
Before commencing installation, the following preliminary checks must be performed:
1) The weight and dimensions
of
the gate must not exceed the limits for use (see the TECHNICAL DATA chap.),
if
they exceed such limits, the operator may not be installed.
2) The gate structure must be suitable for the installation
of
the operator and conform to current standards.
3) The gate’s movement in both opening and closure must be uniform, without points
of
greater resistance or friction.
4) The gate must be properly hung and without risks
of
derailment, this can be checked by sliding the gate back and forth several times.
5) The gate must be hung flat, i.e. it must not move when left in any point
of
the sliding tracks. Ensure that the gate does not bend or deviate from its course during movement.
6) The gate must be perfectly flat in to the plane to which the sliding track
is
fixed, in order to prevent irregular movement during operation.
7) The limit switches must be sufficiently sturdy and there must be no risk
of
derailment should the gate collide with the limit switches.
8) The operator installation area must not be prone to flooding and therefore it may not be installed in potholes, trenches, dips in the ground, etc.
9) The cement base on which the operator must be installed must be adequately solid and compact.
MAINTENANCE INSTRUCTIONS AND WARNINGS
•
Once the automation has been tested, the parameters set must not be altered. If further adjustments (e.g. alterations to the voltage value) are made, all the checks required for testing
and compliance with standards must be repeated.
•
The Manufacturer declines responsibility for damage or injury caused by non-compliance with the information provided in this manual and the safety instructions provided below.
•
The Manufacturer declines all responsibility for damage and malfunctions deriving from non-compliance with the maintenance instructions.
•
In order to keep the operator efficient and safe, follow the cleaning, checking and routine maintenance procedures as described in this manual. This is the owner’s duty.
•
Any checking, maintenance or repair work must be conducted by a PROFESSIONAL FITTER
•
Always switch of the electricity supply in the event of malfunctions, breakdowns and before any other operations in order to avoid the gate from being activated.
•
The owner is not authorised to remove the operator lid as it contains live parts.
•
If the power cable is damaged, it must be replaced by the Manufacturer or its technical Assistance service or in any case a person with a similar qualification in order to avoid risks.
• The owner
is
NOT
authorised to use the programming keyboard.
• Use original pare parts, accessories and clamping material only.
• Do not perform technical or programming modifications on the operator. Operations
of
this type may cause malfunctions and/or risk
of
accidents. The Manufacturer declines responsibility for damage
deriving from modified products.
• In the event
of
intervention
of
automatic or fuse switches, before restoring function conditions identify and eliminate the fault. Request the intervention
of
a
PROFESSIONAL FITTER.
• If
a
fault that cannot be solved following the information contained in the present manual, contact the manufacturer’s assistance service.
• All maintenance, repair or replacement
of
parts must be recorded in the maintenance log, which
is
SUPPLIED AND INITIALLY FILLED IN BY
THE
FITTER.
• Inspect the installation frequently to ensure that there are no signs
of
mechanical unbalance, wear or damage to the wires and assembled parts: no not use the automation until any necessary repairs
or adjustments have been made.
Cleaning the automation
ATTENTION:
•
Never wash the operator using water sprays or washing devices.
•
Do not use corrosive substances, solvents, thinners or spirit to clean the operator.
•
Switch off the electricity supply to the operator before cleaning.
a) Automations are almost always installed outdoors and therefore they are subject to climatic variations and exposed to the elements, which transport debris that may cause problems.
b) The entire area in which the automation
is
installed must be kept clean to avoid malfunctions and/or faults.
c) Keep the track on which the gate runs clean by sweeping stones, gravel, and mud
off
using
a
broom.
d) Clear the area in which the operator is installed to prevent stones, gravel, mud, dry leaves, pine needles etc. from accumulating around the pinion, thus causing damage to the pinion, rack, limit switch and operator.
Routine maintenance
Every six months contact
a
PROFESSIONAL FITTER to perform the following operations.
• A series
of
opening and closing checks using radio controls and selectors, using all the system’s components (photocells, flashing light, etc.). Ensure that the operator performs the desired action.
• Grease the operator’s nut-screw-bushing unit and the gate hinges.
• Repeat the series
of
tests envisaged for operator testing (see INSTALLATION MANUAL
–
Testing and first run chapter.
DEMOLITION AND DISPOSAL
ACER operators are constituted by various materials, which implicates different disposal modes. Materials such
as
aluminium, plastic, electric cables, etc., can be recycled; batteries, electronic cards,
etc. must be disposed of.
ATTENTION:
•
The disposal of batteries, cards and electric and electronic components must comply with legislation and local regulations on toxic, harmful and polluting substances.
•
Disconnection from the main supply must always be performed by a qualified electrician using suitable equipment.
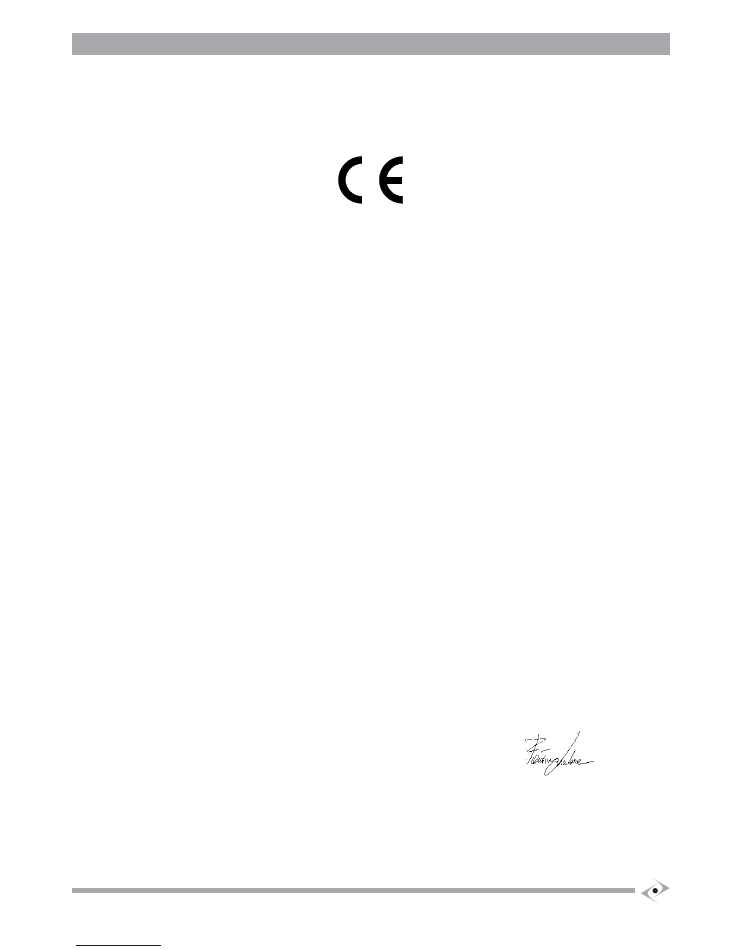
H
SI
L
G
N
E
7
MANUFACTURER’S DECLARATION OF CE CONFORMITY
Declaration of Conformity
under Directive 98/37/EC, appendix II, part B (Manufacturer’s Declaration of CE Conformity).
LIFE home integration
Via 1 Maggio, 37
31043 FONTANELLE (TV) – Italia
declares that the following product:
ACER operator for sliding gates
Satisfies the essential requisites established in the following directives:
• Machinery
Directive 98/37/EC (ex 89/392/EEC) and subsequent amendments,
• Low
voltage directive 73/23/EEC and subsequent amendments,
• Electromagnetic
compatibility directive 89/336/EEC and subsequent amendments,
• Radio
and telecommunications equipment directive 1999/5/EC and subsequent amendments.
and
satisfies
the
following
standards
•
EN 12445:2000 Industrial, commercial and garage doors and gates – Safety in
the
usage of motorised doors – testing
methods.
• EN
12453:2000 Industrial, commercial and garage doors and gates – Safety in
the
usage of motorised doors -
Requisites.
• EN
60204-1:1997
Machinery
safety – Electric equipment of
the
machine
– Part 1: general rules.
• EN
60950 Information
technology
equipment -Safety - Part 1: General requisites.
• ETSI
EN 301489-3:2001 Electromagnetic compatibility for radio equipment and appliances.
• EN
300220-3:2000
Radio
equipment and systems –
short
band devices –
Technical
characteristics
and testing
methods
for radio apparatus
with
a
frequency of 25 to 1000 MHz and
powers
of up to 500mW.
The Manufacturer also declares that it is not permitted for the abovementioned components to be used until such time as the system in which
they are incorporated is declared conform to directive 98/37/EC
.
Fontanelle
Name of Signor:
Faustino Lucchetta
Position:
Managing Director
Signature:
_____________________
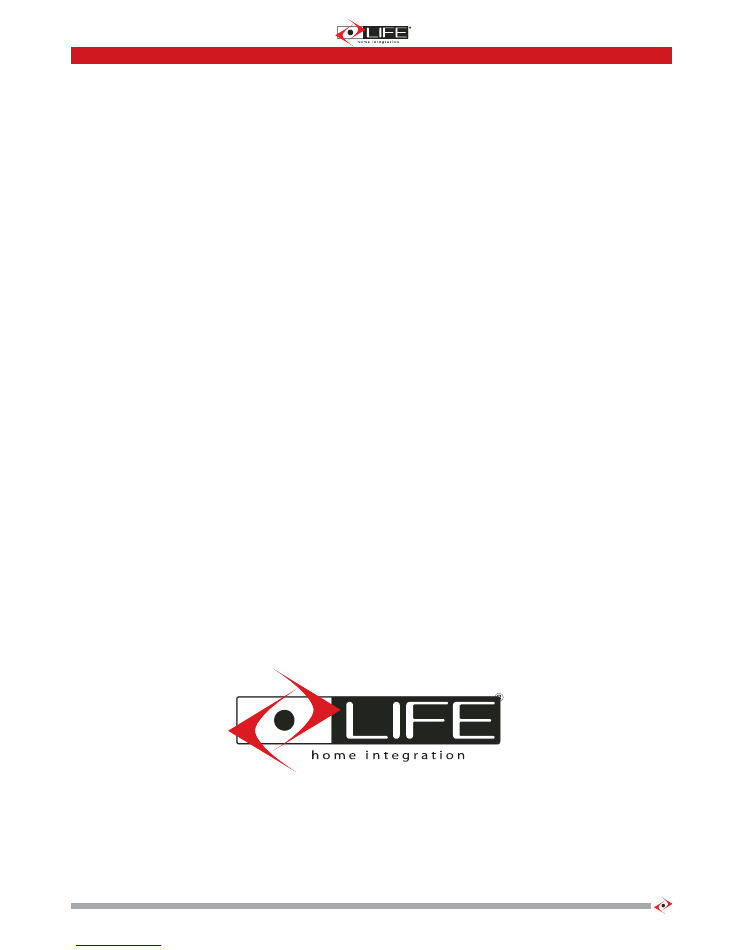
Page 15
Address:
Via Sandro Pertini,3/5 31014 COLLE UMBERTO (TV) Italia
Telephone:
+ 39 0438 388592
Telefax:
+ 39 0438 388593
http
www.homelife.it
e-mail:
info@homelife.it
spot colour
CMYK
Instruction issue V.1