Full Text Searchable PDF User Manual
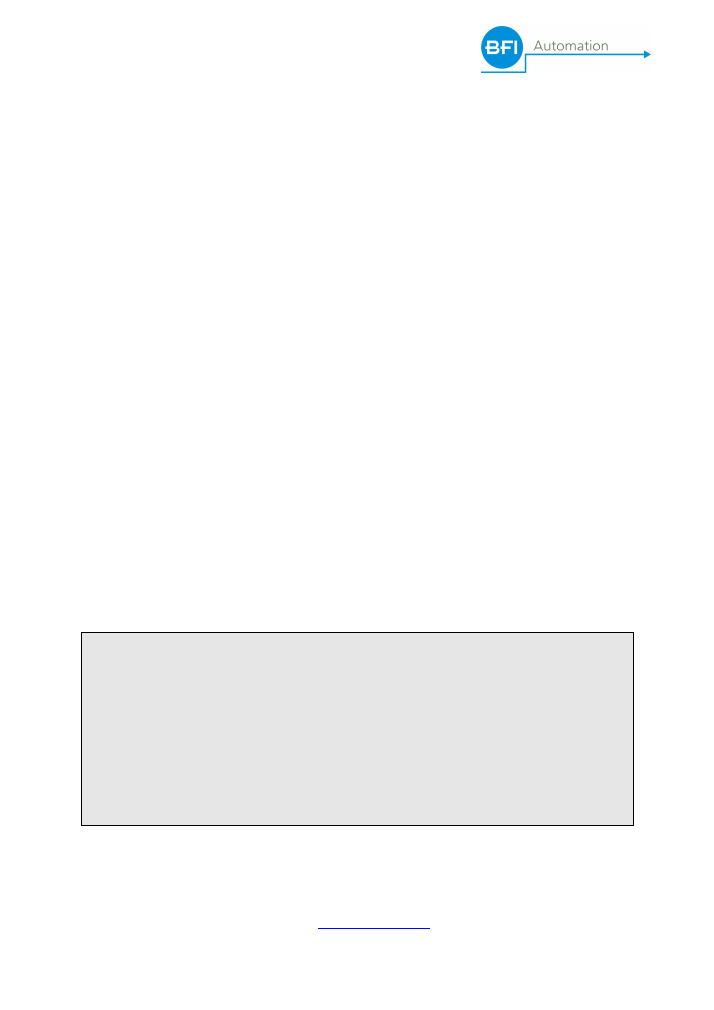
1
COMPACT FLAME CONTROLLER
CFC 200
(Formerly 8.XX)
TECHNICAL DESCRIPTION
EDITION: TB CFC200-REV3-2015-04-07
IMPORTANT:
Please note, that all mounting and wiring as well as all changing or adjustment at
the flame monitoring and evaluation equipment should only be carried out by fully
trained and authorized personnel.
BFI Automation is pleased to support you if you do not have any experience with
the equipment. Our service personnel is carrying out world wide installations, su-
pervision and commissioning and is available upon request.
For the stage of planning you can ask our sales and project engineers for any
support you may need.
BFI Automation is providing any kind of training for your engineers.
PLEASE READ THIS LEAFLET CREFULLY AS IT CONTAINS NECESSARYIN-
FORMATION FOR THE USE OF THIS EQUIPMENT. FOR MORE DETAILED IN-
FORMATION PLEASE REFER TO THE OPERATING AND MAINTENANCE MA-
NUAL.
BFI – Automation Mindermann GmbH, Eggerscheidter Str. 57, D-40883 Ratingen
Phone +49 (0) 2102 96 82 – 0, Fax +49 (0) 2102 9682 – 42
:
info@bfi-automation.de

2
Compact flame controller
CFC 200
-
Flame scanner with integrated flame controller
-
TÜV approved, DIN-DVGW certified
-
CFC 200 UV1 (formerly 8.0) : recommended for pure gas and oil/gas mixture fuels
-
CFC 200 UV (formerly 8.30) : recommended for pure gas and oil/gas mixture fuels
-
CFC 200 IR (formerly 8.40) : recommended for pure oil fuels in diffusion burners
-
CFC 200 IR3 (formerly 8.70): recommended for gas fuels in radiant-surface burners
and for waste gases
-
Adjustable sensitivity
-
Analogue flame intensity output
-
Optical state indication
-
Non-wearing sensors
-
Protection IP 65
!
WARNING
WARNING: IMPROPER INSTALLATION OF THESE PRODUCTS
MAY BE HAZARDOUS TO LIFE AND PROPERTY
Function
The integral method in the respective spectral range is used for the flame radiation analysis of the
compact flame controller.
After pre amplification, the unwanted portion of constant light is withdrawn from the output signal. The
subsequent sensitivity adjustment permits signal suppression for the adaptation to the respective
burner condition.
The subsequently connected band pass filter achieves that modulation of the typical flame radiation of
the primary combustion zone is evaluated only, and outside light signals from neighbouring burners
can be differentiated from the individual burner.
The further functional groups integrate the signal processing for the dynamic monitoring channel,
which, by means of a dark-phase monitoring, continuously checks the failure-safety of the unit.
A component defect leads to an immediate switch-off of the flame-relay, which is available as a poten-
tial-free changeover contact.
The switching state „flame on“ is displayed by a yellow LED on the rear side of the unit, just as the in-
tensity of flame, which is displayed by a flashing green LED.
A flame intensity output 0(4) - 20 mA can be used for external displays. The range can be selected by
jumper see drawing on page 3.
The safety switch-off time, which always depends on the fuels to be detected, is factory adjusted to 1
second. Longer switch-off times in acc. to local specifications available as option.
!
WARNING
WARNING:
The response of the scanner depends on burner configuration
as well as on the turbulence and spectral characteristics of the flames. Ap-
plication assistance is available on request

3
Sensitivity Adjustment
By using a potentiometer which is located on the back side of the compact flame controller beneath a
screw it is easily possible to adapt the controller to various firing conditions.
Turning the potentiometer counter clockwise will reduce the sensitivity. Please note that a reduction of
the sensitivity might also cause a reduction of the current output for the intensity.
Output current selection
Assembly
The correct positioning of the sight tube to the flame with less vibration is an important requirement for
an optimised flame control. The assembly must ensure the primary combustion zone is inside the visi-
ble angle of the flame monitoring device for all loads. This is the only way for discriminating flame con-
trol. The extension of the sight axis may not cross the first third of other flames.
Length and diameter of the sight tube are directly related to the available flame radiation, because the
visibility angle of the device is defined. The maximum length ‘L’ of a sight tube is related to the tube’s
diameter ‘d’.
d
1"
1,5"
2"
L
0,5m
0,8m
1,1m
The tube should be as short as possible. A diameter of 2 inch is recommended.
The right adjustment is shown in the following drawing. The optical adjustment device BFI 235 is
available ex stock (part-no.: P 106)
The compact flame controller is delivered with a flange for quick assembly. The device is equipped
with a supply for purge air which prevents the lens of contamination with dust and a subsequent dam-
age. The optimised assembly kit consists of heating insulator, blocking valve and ball flange.
These mechanical devices are also available on demand.
0-20 mA
4-20mA
Jumper
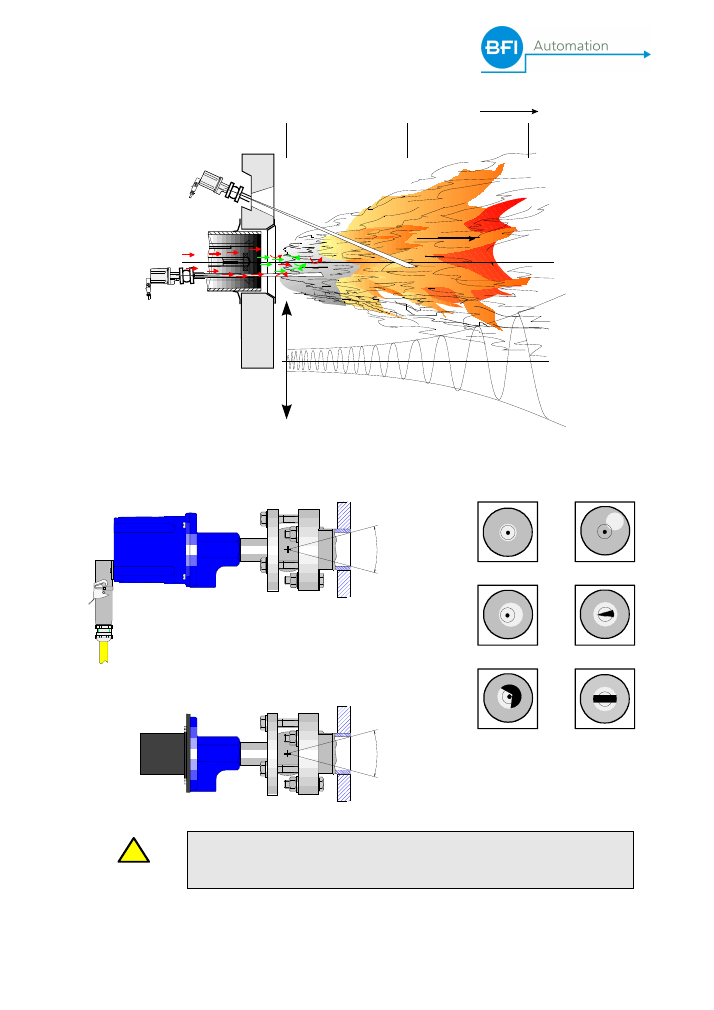
4
!
CAUTION
CAUTION:
All alignment and adjustment procedures should be used when-
ever parts are replaced, when the scanner has been moved, when the flame
shape has altered (additional fuels, new burners, burner/register modifica-
tions), as well as on new installations.
primary air
fuel
flame root
combustion area
changing of frequency and amplitude in
relationship to the distance of the flame root
heating
insulator
optical
adjustment
ball flange
sight tube
mounting flange
flame scanner
adjustment angle
30° max
how to adjust in the right way
right
wrong
░
3
0
°
░
3
0
°
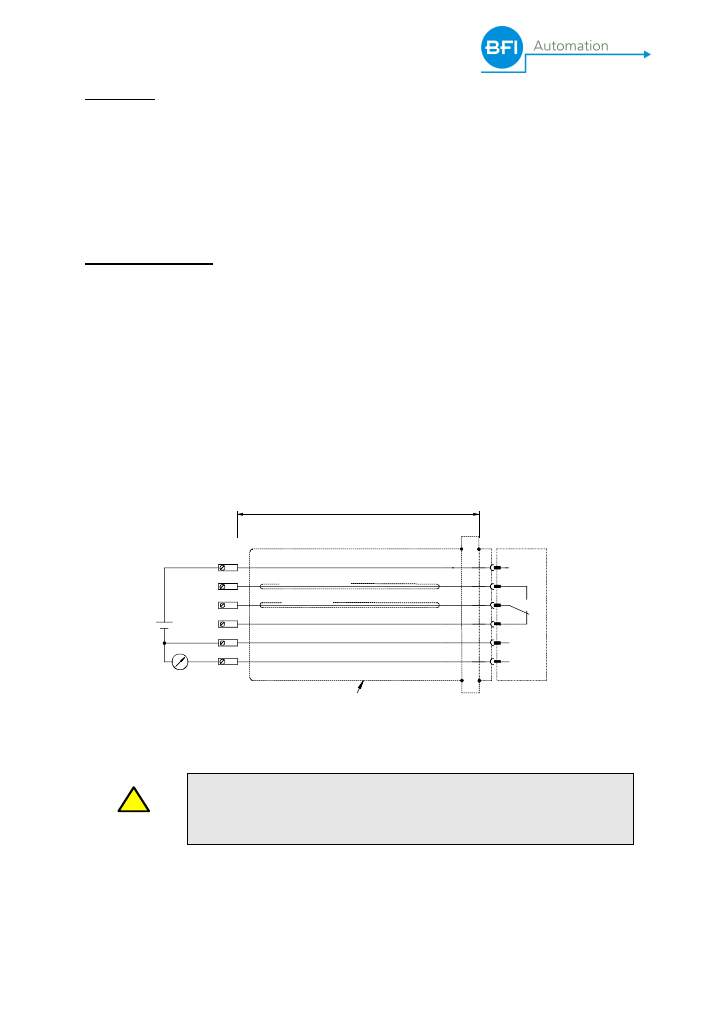
5
Installation
The pin configuration of the plug connector is shown in the terminal connection diagram.
The flame intensity output has no potential separation from the power supply. It is related to the power
supply ground. If there will be any problem in this case an isolation amplifier can be delivered on de-
mand.
A maximum shunt resistance of 250
Ω
should not be exceeded.
The device is immediately ready for operation after switching on the power supply.
!!Do not disconnect the flame controller while energized!!
Connection diagram
Pin/Terminal
Description
Colour of
BFI special cable
KW5
1
Flame relay: supply root
white
2
Flame relay: signal ‘flame ON’
brown
3
Flame relay: signal ‘flame OFF’
pink
4
Power supply: +24 V DC
green
5
Power supply: - 0 V (GND)
yellow
6
Current output: 0(4)-20 mA
grey
!
CAUTION
CAUTION:
On all applications the compact flame controller must be tested
by starting and stopping the burner several times to ensure proper opera-
tion. (e.g.: The flame relay must reliable drop out for all flame conditions.)
The testing should be done with various adjacent burners ON and OFF and
at various load levels. This is a requirement for proper operation.
power supply +24V DC
flame relay "flame ON"
flame relay "root"
flame relay "flame OFF"
power supply 0V (GND)
outer braided shield
current output 0/4 - 20mA
4
2
1
3
4
2
5
6
green
brown
white
pink
yellow
grey
compact-
flame-
controller
6
5
1
3
BFI-special cable KW5
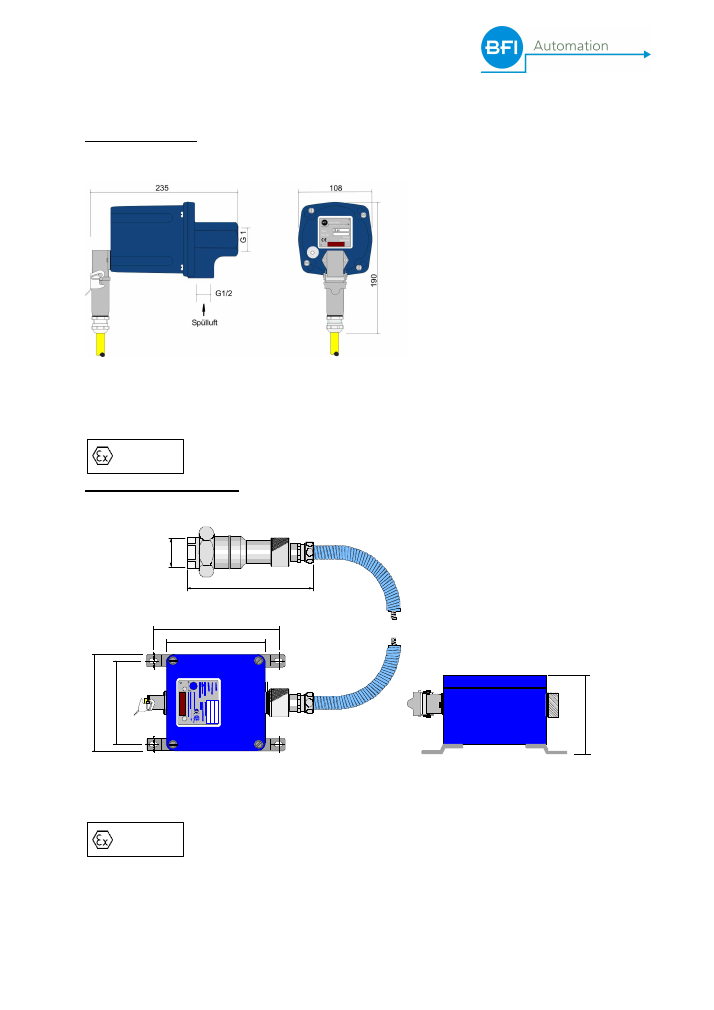
6
8
8
120
1
0
6
152
1
2
2
B
F
I
C
F
C
2
0
0
0
155
G
1
Fibre optic cable
SKL
O/E-Converter
Standard housing
Standard housing suitable for use in hazardous area Zone 2
II 3 G
Ex nA II T4
OE-Converter housing
Suitable for use in hazardous areas Zone 2
II 3 G
Ex nA II T4

7
2 8 6
G
1
Ø
1
2
0
Empfindlichkeits-
einstellung
LED grün = Intensität
LED gelb = Flamme "EIN"
Ø13
232
262
304
1
4
2
1
6
6
.5
1
9
5
.5
2
3
2
1
4
0044
Type 07-6152-9016
II 2G Ex de IIC T6
II 2D Ex tD A22 IP 65 T 80°C
0044
Type 07-4160-1165/5003
II 2G Ex de IIC T6 Gb
II 2D Ex tb IIIC T 80° Db
Ex-proofed housing
For areas classified as Zone I
PTB 03 ATEX 1051
Explosion Proof Housing for OE-Converter
For one OE-Converter
For use in hazardous areas classified as Zone 1
KEMA 08 ATEX 0123
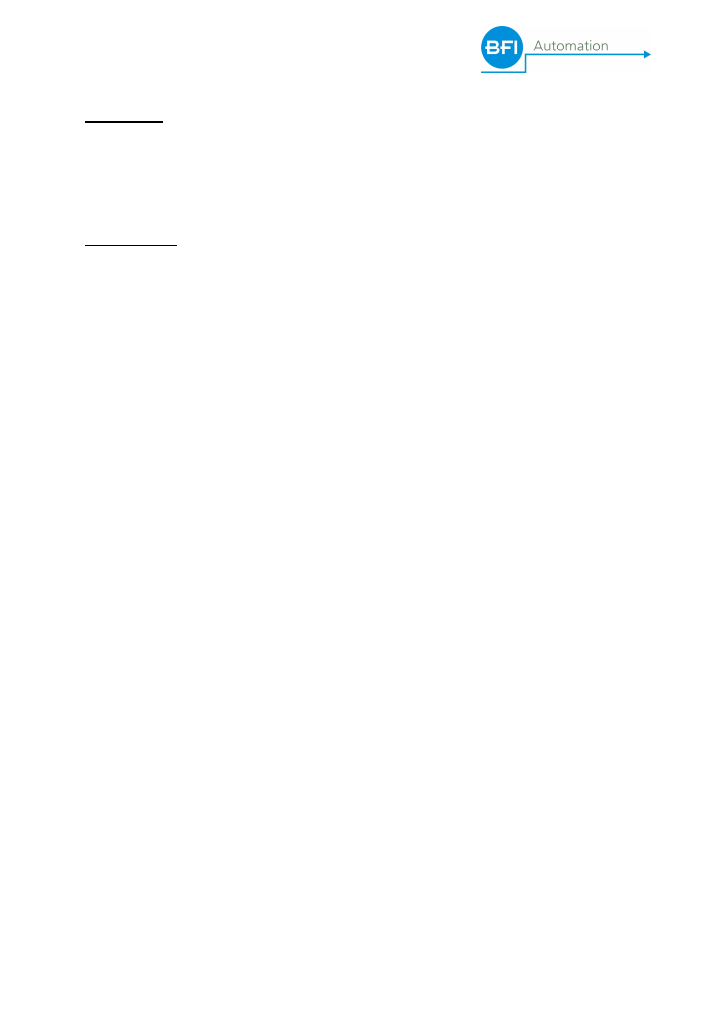
8
Accessories
Power supply 230/115V AC
Swivel mount 1 inch and 2 inch flange disk
Heating insulator 1 inch
3-way ball cock 1 inch
Pressure screw joint 5bar size 1 inch
Optical adjusting device
Technical data
Spectral sensitivity
CFC 200 UV1 (formerly 8.0)
190 up to 550 nm
CFC 200 UV (formerly 8.30)
280 up to 420 nm
CFC 200 IR (formerly 8.40)
300 up to 1050 nm
CFC 200 IR3 (formerly 8.70)
1050 up to 2700 nm
Visual aperture
2.7 degrees
Input voltage
24 V DC
Current consumption
approx. 200 mA
Construction
according to SELV III
Ambient temperature
-20°C...+70°C
Current output
0(4)...20 mA (Ra < 250 Ohm) flame intensity
Flame relay
1 change-over contact, potential free
VDE 0110, Class A
max. 48 V switching voltage
max. 1 A switching current (fused with 0.5 A)
max. 30 W switching power
switching point "flame on"5(8) mA
switching point "flame off"< 5(8) mA
Flame failure response time,
1 second, factory preset
switch-off time
other switch off times on request
Sight tube connection
1" internal thread ISO 228
Purge air connection
1/2" internal thread ISO 228
Purge air quantity
10 m
3
/h at standard conditions
Electrical connection
Standard
Harting connector HAN8 90 degrees
Flame proof housing
3m special cable
OE-Converter
Harting connector HAN8 90 degrees
EX-OE-Converter
M20-screw joint and terminal clamps inside
Dimension
Standard with flange
235 x 108 mm (Length x Diameter)
Explosion proof housing
223 x 120 mm (Length x Diameter)*
OE-Converter housing
120 x 122 x 80mm (Length x Width x Height)*
Ex-OE-Converter housing
232 x 232 x 166,5mm (Length x Width x Height)*
Triple Ex-OE-Converter
276 x 276 x 218mm (Length x Width x Height)*
*without plugs and mounting bracket
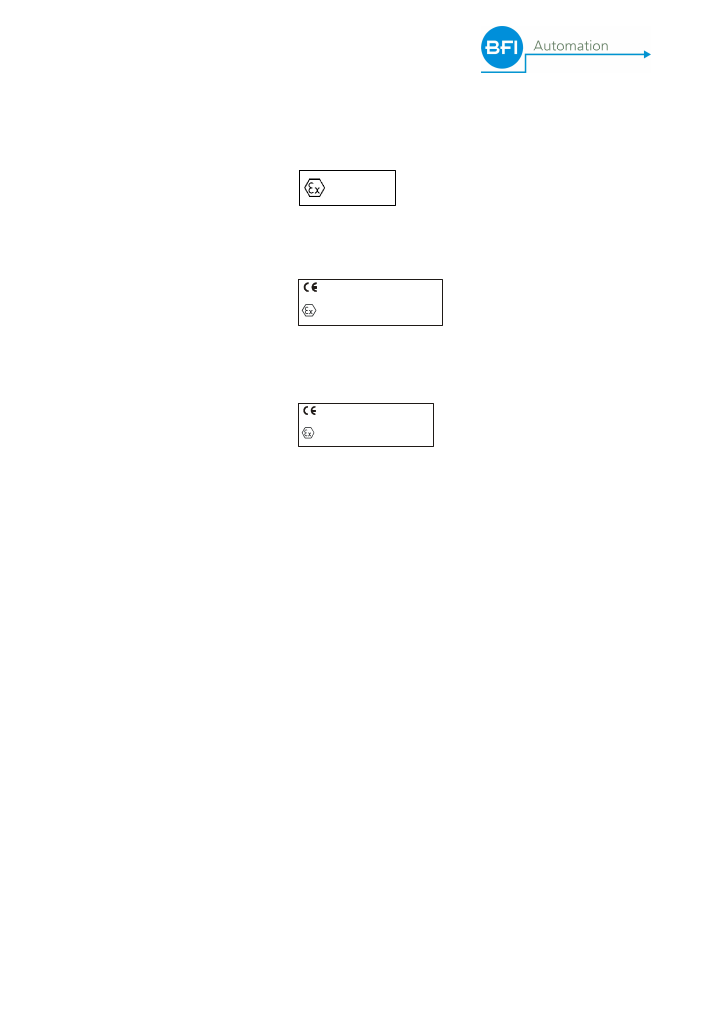
9
0044
Type 07-6152-9016
II 2G Ex de IIC T6
II 2D Ex tD A22 IP 65 T 80°C
0044
Type 07-4160-1165/5003
II 2G Ex de IIC T6 Gb
II 2D Ex tb IIIC T 80° Db
Class of protection
Standard and OE-Converter housing IP 65, similar to NEMA
4/Class 1 Div 2
ATEX Zone 2
II 3 G
Ex nA II T4
Ex proof housing IP66, similar to NEMA 4/Class 1 Div 1
ATEX Zone 1
PTB 03 ATEX 1051
Ex-OE-Converter housing
ATEX Zone 1
KEMA 08 ATEX 0123
Weight
Standard
1.5 kg
Explosion proof housing
4.0 kg
OE-Converter housing
1.5 kg
Ex-OE-Converter housing
7.0 kg
Triple Ex-OE-Converter h.
13.0 kg
Electronic self-monitoring for the fail-safe function control of the device according VDE 0116,
EN 298:2012, and TRD 411 to 414. DIN-DVGW approved and CE conformity.
Certified to CSA standards.
Rights for technical changes reserved
© BFI AUTOMATION 2015